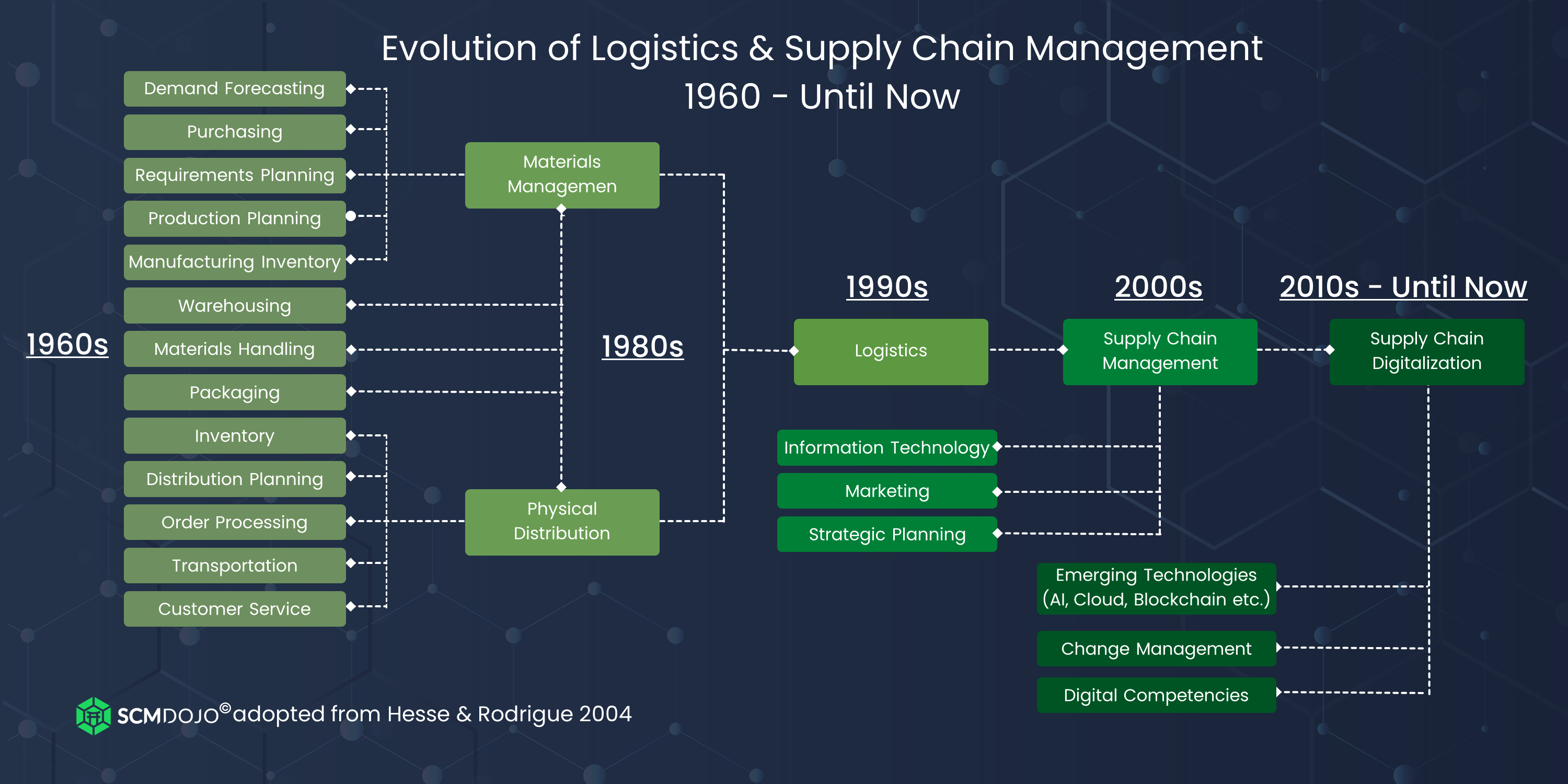
Apparel manufacturers today face a unique challenge in meeting the diverse demands of their customers. These consumers have different physiographic, socioeconomic, and demographic characteristics, so it is difficult to predict their preferences. Information is also easier to access as consumers are more aware of the differences between products. At the same time, they are becoming more inclined to buy expensive, high-fashion items.
Production efficiency
Increasing production efficiency in apparel manufacture is a key element in the overall strategy of apparel manufacturers. The clothing industry is highly dependent on human labor, and with ever-changing fashion trends, production planning is essential to meet the needs of consumers and the marketplace. As a result, apparel manufacturers must ensure they can adapt to global requirements and meet a short product development cycle. In addition to planning for new products, apparel manufacturers should evaluate the efficiency of their existing lines and implement digital technologies, which can reduce the product development cycle from months to days. The planning process should include critical path analysis.
It is possible to increase the efficiency of apparel manufacturing, despite it being labor-intensive. However, achieving this goal requires a combination of the right tools and proper management. A simple increase in efficiency of 10 to 15 percent can translate into a 3-5% increase to EBITDA. Moreover, efficiency increases workers' wages and can improve the country's ability to compete in the global market.
Fabric layering
Fabric layering is an apparel manufacturing technique. It involves placing a pre-made pattern on top of a lay. You can either use a plotter or hand to create the pattern. The pattern components are laid in markers. They are then cut with a straight knife, or another cutting method.
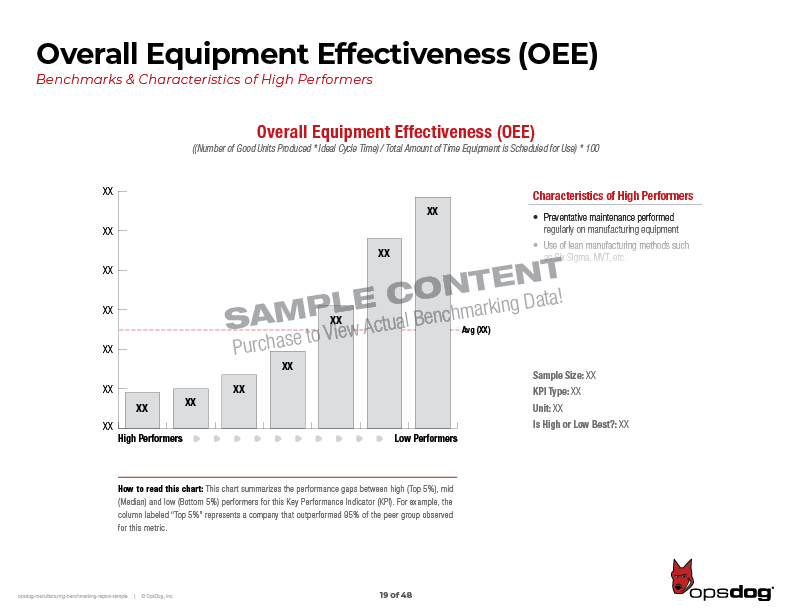
During this process, the fabric is spread evenly. It can be laid out in a pile or laid out in superimposed layers with the cutting marker on top. The maximum cutting width is the fabric width that is usable, minus any selvedges or needle marks. The fabric utilization refers to the amount of fabric used. The two types of layout are half-garment lay and whole-garment lay. Half-garment Lay involves placing fabric on only one side of a garment piece. Whole-garment Lay involves covering fabric on both sides. The drawback to the whole garment layout is its greater fabric consumption.
Cutting
Cutting involves using cutting blades that cut a particular piece of fabric into smaller pieces. Fabric can cost between 60 and 70 percent of a garment's price. It is crucial that every inch be used. Using a strict control system in apparel manufacturing will ensure that every inch of fabric is utilized.
Spreading fabric onto a large surface is the first step to cutting fabric. In mass production, the fabric is spread over a number layers. Based on the number of garments that will be produced and the thickness of fabric, the cutting master determines the appropriate layer count. After the fabric has been spread it is measured to determine the maximum cutting width.
Pressing
Pressing is an important process in the manufacture of apparel. It controls the appearance of garments and helps them to maintain their comfort. This is done in a factory. Automated or manual operation can be used to operate a press. Software can be used for controlling the automation level. Software can be used to program a press to follow certain instructions. Automation of pressing in an apparel manufacturing factory can reduce the possibility of human error. The increasing number of fibers and fabric varieties will require more precise control of temperature and pressure during the process.
Pressing refers to using heat to soften the fibers. The garment's shape will be stabilized by softened fibers. To avoid damage to the yarns or fibers, it is important that you choose the right temperature.
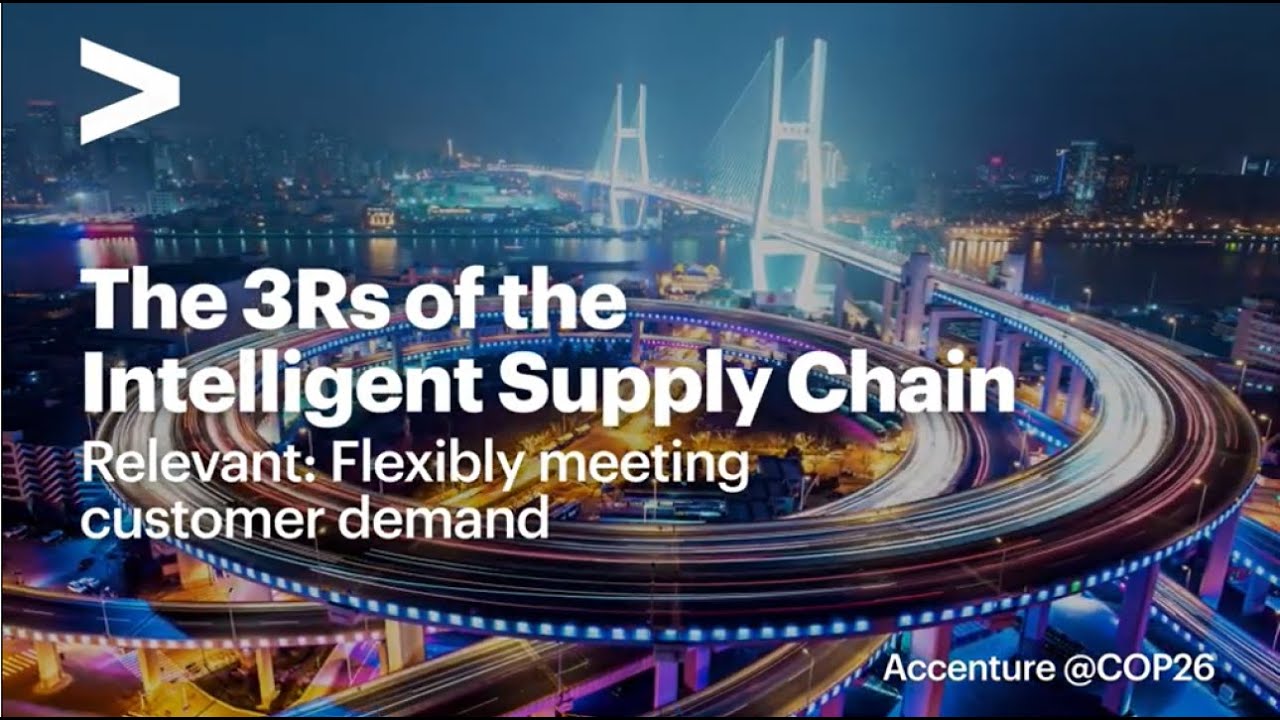
Minimum order quantity
If you're looking for a clothing manufacturer to source from, it is important that you know what the Minimum Order Quantity (or MOQ) of the factory you are interested in. This minimum order quantity is required by many garment factories. The MOQ can vary from factory to factory depending on the technical characteristics and design of your garments. Some factories are able to accept orders up to 100 items. Others require orders over a thousand.
Most manufacturers need to have a minimum order quantity (MOQ), especially if they deal in bulk products. This quantity helps them to remain profitable and weeds out businesses that want to purchase items in small quantities but aren't necessarily looking to place a large order. This is particularly important for custom orders.
FAQ
What is production planning?
Production Planning is the creation of a plan to cover all aspects, such as scheduling, budgeting. Location, crew, equipment, props and other details. This document is designed to make sure everything is ready for when you're ready to shoot. It should also provide information about how best to produce the best results while on set. This includes information on shooting times, locations, cast lists and crew details.
First, you need to plan what you want to film. You may have already decided where you would like to shoot, or maybe there are specific locations or sets that you want to use. Once you have identified your locations and scenes it's time to begin figuring out what elements you will need for each one. You might decide you need a car, but not sure what make or model. You could look online for cars to see what options are available, and then narrow down your choices by selecting between different makes or models.
After you've found the perfect car, it's time to start thinking about adding extras. Are you looking for people to sit in the front seats? Perhaps you have someone who needs to be able to walk around the back of your car. You may want to change the interior's color from black or white. These questions will help determine the look and feel you want for your car. Another thing you can do is think about what type of shots are desired. What type of shots will you choose? Maybe you want the engine or the steering wheels to be shown. This will allow you to determine the type of car you want.
Once you have made all the necessary decisions, you can start to create a schedule. You can create a schedule that will outline when you must start and finish your shoots. You will need to know when you have to be there, what time you have to leave and when your return home. So everyone is clear about what they need to do. Hire extra staff by booking them ahead of time. It's not worth paying someone to show up if you haven't told him.
Also, consider how many days you will be filming your schedule. Some projects can be completed in a matter of days or weeks. Others may take several days. You should consider whether you will need more than one shot per week when creating your schedule. Shooting multiple takes over the same location will increase costs and take longer to complete. You can't be certain if you will need multiple takes so it is better not to shoot too many.
Budgeting is another important aspect of production planning. As it will allow you and your team to work within your financial means, setting a realistic budget is crucial. It is possible to reduce the budget at any time if you experience unexpected problems. However, it is important not to overestimate the amount that you will spend. You will end up spending less money if you underestimate the cost of something.
Production planning is a detailed process. But, once you understand the workings of everything, it becomes easier for future projects to be planned.
How can overproduction in manufacturing be reduced?
Improved inventory management is the key to reducing overproduction. This would reduce the time needed to manage inventory. By doing this, we could free up resources for other productive tasks.
This can be done by using a Kanban system. A Kanbanboard is a visual tool that allows you to keep track of the work being done. Kanban systems allow work items to move through different states until they reach their final destination. Each state represents an individual priority level.
When work is completed, it can be transferred to the next stage. However, if a task is still at the beginning stages, it will remain so until it reaches the end of the process.
This allows for work to continue moving forward, while also ensuring that there is no work left behind. A Kanban board allows managers to monitor how much work is being completed at any given moment. This data allows them adjust their workflow based upon real-time data.
Lean manufacturing is another option to control inventory levels. Lean manufacturing works to eliminate waste throughout every stage of the production chain. Anything that does not contribute to the product's value is considered waste. Some common types of waste include:
-
Overproduction
-
Inventory
-
Packaging that is not necessary
-
Overstock materials
By implementing these ideas, manufacturers can improve efficiency and cut costs.
What is the difference in Production Planning and Scheduling, you ask?
Production Planning (PP) is the process of determining what needs to be produced at any given point in time. This is accomplished by forecasting the demand and identifying production resources.
Scheduling is the process that assigns dates to tasks so they can get completed within a given timeframe.
What is the responsibility for a logistics manager
Logistics managers are responsible for ensuring that all goods arrive in perfect condition and on time. This is done through his/her expertise and knowledge about the company's product range. He/she should make sure that enough stock is on hand to meet the demands.
What are the four types of manufacturing?
Manufacturing is the process by which raw materials are transformed into useful products through machines and processes. It includes many different activities like designing, building and testing, packaging, shipping and selling, as well as servicing.
Is it possible to automate certain parts of manufacturing
Yes! Yes! Automation has existed since ancient times. The Egyptians invented the wheel thousands of years ago. Robots are now used to assist us in assembly lines.
There are many uses of robotics today in manufacturing. These include:
-
Line robots
-
Robot welding
-
Robot painting
-
Robotics inspection
-
Robots that create products
Manufacturing can also be automated in many other ways. 3D printing makes it possible to produce custom products in a matter of days or weeks.
Statistics
- In 2021, an estimated 12.1 million Americans work in the manufacturing sector.6 (investopedia.com)
- You can multiply the result by 100 to get the total percent of monthly overhead. (investopedia.com)
- Job #1 is delivering the ordered product according to specifications: color, size, brand, and quantity. (netsuite.com)
- [54][55] These are the top 50 countries by the total value of manufacturing output in US dollars for its noted year according to World Bank.[56] (en.wikipedia.org)
- (2:04) MTO is a production technique wherein products are customized according to customer specifications, and production only starts after an order is received. (oracle.com)
External Links
How To
How to Use lean manufacturing in the Production of Goods
Lean manufacturing (or lean manufacturing) is a style of management that aims to increase efficiency, reduce waste and improve performance through continuous improvement. It was created in Japan by Taiichi Ohno during the 1970s and 80s. He received the Toyota Production System award (TPS), from Kanji Toyoda, founder of TPS. Michael L. Watkins published the book "The Machine That Changed the World", which was the first to be published about lean manufacturing.
Lean manufacturing is often described as a set if principles that help improve the quality and speed of products and services. It emphasizes reducing defects and eliminating waste throughout the value chain. Lean manufacturing is called just-in-time (JIT), zero defect, total productive maintenance (TPM), or 5S. Lean manufacturing emphasizes reducing non-value-added activities like inspection, rework and waiting.
Lean manufacturing improves product quality and costs. It also helps companies reach their goals quicker and decreases employee turnover. Lean Manufacturing is one of the most efficient ways to manage the entire value chains, including suppliers and customers as well distributors and retailers. Lean manufacturing is widely practiced in many industries around the world. Toyota's philosophy, for example, is what has enabled it to be successful in electronics, automobiles, medical devices, healthcare and chemical engineering as well as paper and food.
Five basic principles of Lean Manufacturing are included in lean manufacturing
-
Define Value - Determine the value that your business brings to society. Also, identify what sets you apart from your competitors.
-
Reduce Waste – Eliminate all activities that don't add value throughout the supply chain.
-
Create Flow - Ensure work moves smoothly through the process without interruption.
-
Standardize and simplify – Make processes as repeatable and consistent as possible.
-
Build relationships - Develop and maintain personal relationships with both your internal and external stakeholders.
Although lean manufacturing has always been around, it is gaining popularity in recent years because of a renewed interest for the economy after 2008's global financial crisis. Many companies have adopted lean manufacturing methods to increase their marketability. Some economists even believe that lean manufacturing can be a key factor in economic recovery.
Lean manufacturing is becoming a popular practice in automotive. It has many advantages. These include improved customer satisfaction, reduced inventory levels, lower operating costs, increased productivity, and better overall safety.
The principles of lean manufacturing can be applied in almost any area of an organization. Lean manufacturing is most useful in the production sector of an organisation because it ensures that each step in the value-chain is efficient and productive.
There are three main types in lean manufacturing
-
Just-in Time Manufacturing, (JIT): This kind of lean manufacturing is also commonly known as "pull-systems." JIT stands for a system where components are assembled on the spot rather than being made in advance. This strategy aims to decrease lead times, increase availability of parts and reduce inventory.
-
Zero Defects Manufacturing (ZDM),: ZDM is a system that ensures no defective units are left the manufacturing facility. Repairing a part that is damaged during assembly should be done, not scrapping. This applies to finished goods that may require minor repairs before shipment.
-
Continuous Improvement (CI: Continuous improvement aims to increase the efficiency of operations by constantly identifying and making improvements to reduce or eliminate waste. Continuous Improvement (CI) involves continuous improvement in processes, people, tools, and infrastructure.