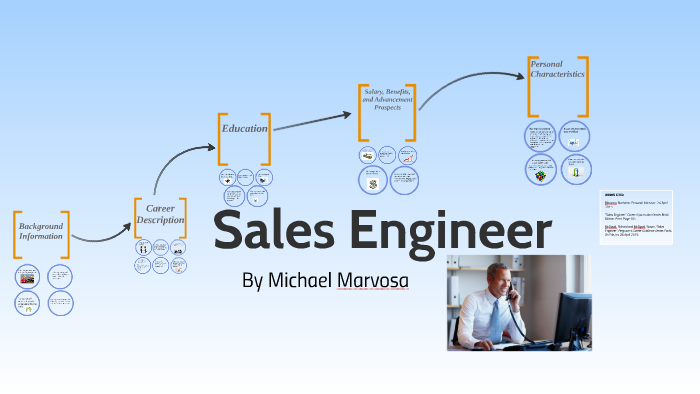
US manufacturing is our largest and most dynamic industry. It's a major driver of economic growth. Its annual output generates around $2 trillion for the United States, creating jobs and supporting hundreds local economies.
Since the global financial crisis, we have seen a dramatic decline in manufacturing employment. The underlying problems - the loss in American jobs to China, and the trade deficit that results - may be difficult to understand. However, it is clear that this has had a significant impact on the overall economy.
The US manufacturing economy supports an estimated 17 million jobs, and its output adds a significant contribution to the US GDP. It is a vital part of our economy. It accounts 20 percent for our capital expenditure, 35 percent for productivity growth, 60% of exports, 70% of R&D spend by businesses (Exhibit 1 ).
While these industries have seen declines and disruptions in many cases, the US Manufacturing sector is currently undergoing a massive transformation. It is being challenged by low-cost producers in Asia, and it may be poised for an overhaul that could help US growth rebound.
Rebuilding the manufacturing sector after it has been battered will require a committed long-term effort to support both the industry and its people. This will include a commitment to support the workforce, as well as innovation, technology and infrastructure.
We must build a more innovative, competitive manufacturing industry to allow our economy to thrive and compete. It is not just a project for a year, but an ongoing commitment over a number of decades to rebuild the strength and innovation in our manufacturing industry.
A strong and durable manufacturing economy can provide employment for large segments of the population. It can also unlock important advancement paths and deliver goods and services with added value that help strengthen our economies. It can also help recalibrate the US economy, bolster our middle class and improve the lives of millions of Americans.
There are several ways to strengthen the manufacturing industry, and there are also many programs that can help us achieve this goal. We have a manufacturing council that advises the secretary of commerce and government agencies on policies that affect the manufacturing sector, and we have many other federal departments and organizations that are actively engaged in supporting our manufacturers.
Manufacturing is a major economic engine for the country. It creates jobs and drives growth in some of its most diverse communities. It is a sector that employs a wider than average swath and allows workers to upgrade their skills without a four year degree.
The average earnings of workers without a college degree in manufacturing, for example, are 10.9 percent greater than the average earnings of workers with a similar education in the overall economy. This has helped to rebalance the distribution of income and wealth in the U.S. The manufacturing sector was also a key route for the poor to rise up the economic ladder.
FAQ
What is the responsibility of a production planner?
A production planner ensures all aspects of the project are delivered on time, within budget, and within scope. They make sure that the product and services meet client expectations.
What is the best way to learn about manufacturing?
You can learn the most about manufacturing by getting involved in it. However, if that's not possible, you can always read books or watch educational videos.
What are the logistics products?
Logistics refers to the movement of goods from one place to another.
They include all aspects associated with transport including packaging, loading transporting, unloading storage, warehousing inventory management customer service, distribution returns and recycling.
Logisticians make sure that the right product arrives at the right place at the correct time and in safe conditions. Logisticians help companies improve their supply chain efficiency by providing information about demand forecasts and stock levels, production schedules, as well as availability of raw materials.
They can also track shipments in transit and monitor quality standards.
What are the 7 Rs of logistics management?
The 7R's of Logistics is an acronym for the seven basic principles of logistics management. It was created by the International Association of Business Logisticians and published in 2004 under its "Seven Principles of Logistics Management".
The following letters make up the acronym:
-
Responsive - ensure all actions are legal and not harmful to others.
-
Reliable - have confidence in the ability to deliver on commitments made.
-
Reasonable - use resources efficiently and don't waste them.
-
Realistic - Take into consideration all aspects of operations including cost-effectiveness, environmental impact, and other factors.
-
Respectful: Treat others with fairness and equity
-
Reliable - Find ways to save money and increase your productivity.
-
Recognizable provides value-added products and services to customers
What is the responsibility of a logistics manager?
A logistics manager ensures that all goods are delivered on time and without damage. This is done by using his/her experience and knowledge of the company's products. He/she also needs to ensure adequate stock to meet demand.
Statistics
- According to a Statista study, U.S. businesses spent $1.63 trillion on logistics in 2019, moving goods from origin to end user through various supply chain network segments. (netsuite.com)
- In the United States, for example, manufacturing makes up 15% of the economic output. (twi-global.com)
- In 2021, an estimated 12.1 million Americans work in the manufacturing sector.6 (investopedia.com)
- You can multiply the result by 100 to get the total percent of monthly overhead. (investopedia.com)
- Many factories witnessed a 30% increase in output due to the shift to electric motors. (en.wikipedia.org)
External Links
How To
Six Sigma: How to Use it in Manufacturing
Six Sigma refers to "the application and control of statistical processes (SPC) techniques in order to achieve continuous improvement." Motorola's Quality Improvement Department, Tokyo, Japan, developed it in 1986. Six Sigma's core idea is to improve the quality of processes by standardizing and eliminating defects. Since there are no perfect products, or services, this approach has been adopted by many companies over the years. Six Sigma aims to reduce variation in the production's mean value. This means that if you take a sample of your product, then measure its performance against the average, you can find out what percentage of the time the process deviates from the norm. If it is too large, it means that there are problems.
The first step toward implementing Six Sigma is understanding how variability works in your business. Once you have a good understanding of the basics, you can identify potential sources of variation. This will allow you to decide if these variations are random and systematic. Random variations occur when people do mistakes. Symmetrical variations are caused due to factors beyond the process. For example, if you're making widgets, and some of them fall off the assembly line, those would be considered random variations. You might notice that your widgets always fall apart at the same place every time you put them together.
Once you have identified the problem, you can design solutions. It might mean changing the way you do business or redesigning it entirely. Test them again once you've implemented the changes. If they don’t work, you’ll need to go back and rework the plan.