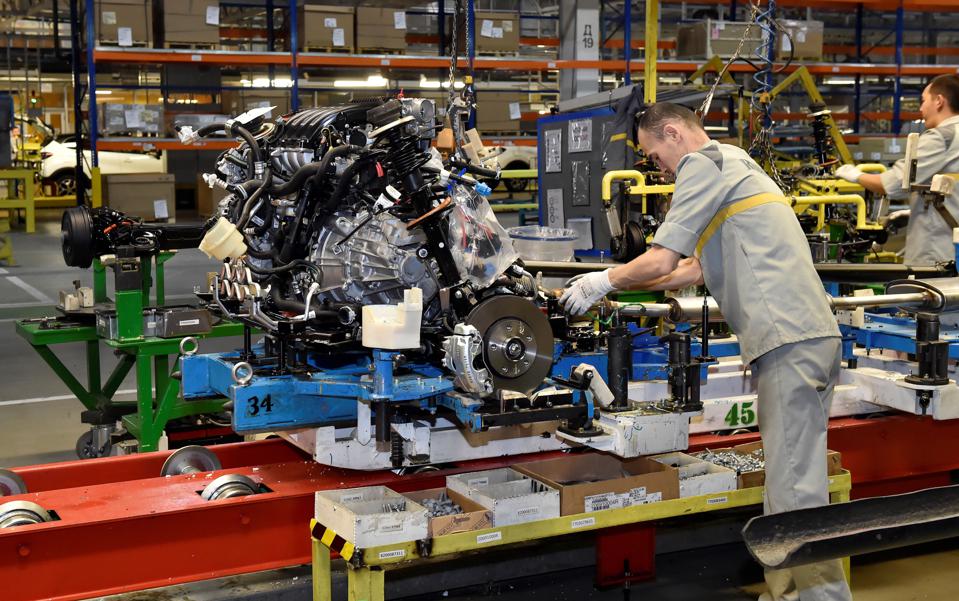
A director of manufacturing manages the company's entire manufacturing process. They are responsible for overseeing all aspects of manufacturing, from design through to production. For this job, you must have a great deal of manufacturing experience and be familiar with all new technologies. These technologies include 3D printing and robotics. It is a benefit to a director who stays current with the latest technologies. As the manufacturing industry develops, the director's position will become more complex as he or she must collaborate with engineering and operations as well as place greater emphasis on quality assurance within the plant.
Salary for a director in manufacturing
The pay scale for a Director of Manufacturing depends on where they live. Many directors earn in the six-figures range. Some directors make significantly more than others. A Director of Manufacturing's salary can vary depending on education and years of experience. In order to determine how much you'll earn in your area, consider a few factors that may influence your salary:
Although the salary of a Director of Manufacturing is variable, it is generally higher for those with more experience. Pay can be affected by your location and cost of living. A large city may offer higher salaries. However, you should be aware of the fact that your salary may not cover living costs. It is important that you are always willing to negotiate a higher salary when the opportunity arises.
The annual salary of a Director of Manufacturing Operations is between $181,500 to $66,000. The salary for a Director of Manufacturing Operations is highly variable and can vary by up to 8% between different cities. A director of manufacturing operations in Fremont, CA can earn between $128,493 and $164,500, which is considerably more than the national average. However, the salary for a Director of Manufacturing Operations varies greatly depending on the location, experience level, and company.
Education required
Director of manufacturing is responsible to manage a manufacturing facility and supervise the production process. The director of manufacturing is responsible for hiring new workers, overseeing quality control, working with designers, as well as meeting operational standards. A director of manufacturing usually reports to the top management team. He or she executes sales and policy initiatives. Candidates must have some manufacturing experience and be able communicate well. There are different educational requirements to become a director in manufacturing.
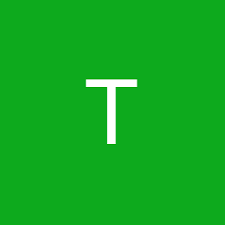
While a degree in engineering is not required for director-level manufacturing jobs, it will help you to build your knowledge and skills. An MBA program is an excellent choice for this role, since it allows candidates to learn more about management, business administration, and economics. You will eventually be responsible to manage a diverse group.
As a director in manufacturing you will work closely alongside engineers and designers during the product design phase. You will participate in the evaluation of new processes and setting quality standards before investing resources into larger productions. Successful directors are also responsible for overseeing the production process and acting as coaches for their employees. They will coach them in best practices and risk mitigation. Manufacturing directors are responsible for overseeing all aspects of production and must also have problem-solving skills.
Experience required
A bachelor's degree in a relevant field and five to 10 years of progressive work experience are often necessary for this position. Generally, manufacturing companies prefer to hire internal employees for this role. The ideal candidate must have a deep understanding of the manufacturing industry and its business goals. Some employers may prefer a graduate certificate. Candidates may also need additional training in the chosen industry or field.
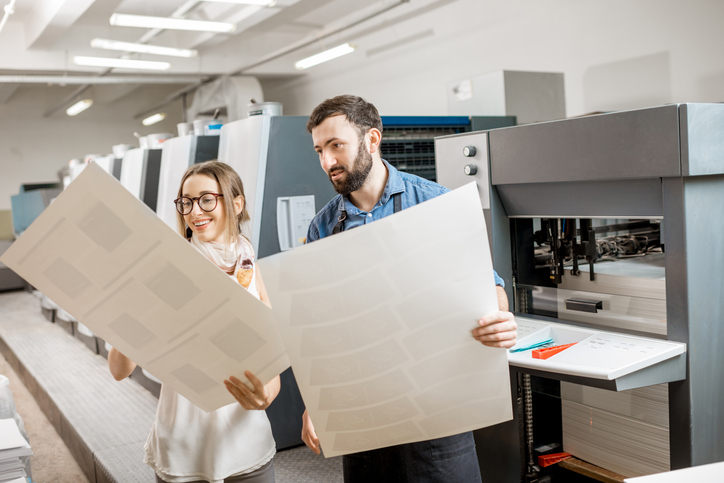
The manufacturing director oversees all aspects of the production process including workers, supervisors and engineers. They could be responsible to solve problems and develop solutions. They might also be responsible to develop and implement quality control programs. Directly reporting to the head of manufacturing, a director of manufacturing is responsible for developing and implementing quality-control programs. Experience in manufacturing is essential. Experience in manufacturing management can help you succeed in this position.
It is important to have experience as a director in manufacturing. Director must have at minimum 10 years experience in a manufacturing environment. These individuals may have had previous experience as managers or technicians. They should have excellent communication skills. The director of manufacturing must also be able to understand business strategy. A director of Manufacturing must also be able to communicate effectively with other departments. In this capacity, the director oversees the production process and ensures that it meets the highest quality standards.
FAQ
What is the responsibility of a logistics manager?
Logistics managers are responsible for ensuring that all goods arrive in perfect condition and on time. This is achieved by using their knowledge and experience with the products of the company. He/she also needs to ensure adequate stock to meet demand.
What is the difference between Production Planning, Scheduling and Production Planning?
Production Planning (PP), or production planning, is the process by which you determine what products are needed at any given time. Forecasting and identifying production capacity are two key elements to this process.
Scheduling refers the process by which tasks are assigned dates so that they can all be completed within the given timeframe.
How can manufacturing overproduction be reduced?
Improved inventory management is the key to reducing overproduction. This would reduce the time needed to manage inventory. This could help us free up our time for other productive tasks.
One way to do this is to adopt a Kanban system. A Kanban Board is a visual display that tracks work progress. In a Kanban system, work items move through a sequence of states until they reach their final destination. Each state represents a different priority level.
For instance, when work moves from one stage to another, the current task is complete enough to be moved to the next stage. But if a task remains in the beginning stages it will stay that way until it reaches its end.
This allows work to move forward and ensures that no work is missed. Managers can monitor the work being done by Kanban boards to see what is happening at any given time. This information allows them to adjust their workflow based on real-time data.
Another way to control inventory levels is to implement lean manufacturing. Lean manufacturing seeks to eliminate waste from every step of the production cycle. Anything that doesn't add value to the product is considered waste. There are several types of waste that you might encounter:
-
Overproduction
-
Inventory
-
Packaging that is not necessary
-
Exceed materials
By implementing these ideas, manufacturers can improve efficiency and cut costs.
What are manufacturing and logistics?
Manufacturing is the production of goods using raw materials. Logistics manages all aspects of the supply chain, including procurement, production planning and distribution, inventory control, transportation, customer service, and transport. Logistics and manufacturing are often referred to as one thing. It encompasses both the creation of products and their delivery to customers.
Statistics
- Many factories witnessed a 30% increase in output due to the shift to electric motors. (en.wikipedia.org)
- Job #1 is delivering the ordered product according to specifications: color, size, brand, and quantity. (netsuite.com)
- [54][55] These are the top 50 countries by the total value of manufacturing output in US dollars for its noted year according to World Bank.[56] (en.wikipedia.org)
- In 2021, an estimated 12.1 million Americans work in the manufacturing sector.6 (investopedia.com)
- In the United States, for example, manufacturing makes up 15% of the economic output. (twi-global.com)
External Links
How To
How to Use 5S to Increase Productivity in Manufacturing
5S stands for "Sort", 'Set In Order", 'Standardize', & Separate>. The 5S methodology was developed at Toyota Motor Corporation in 1954. It improves the work environment and helps companies to achieve greater efficiency.
The idea behind standardizing production processes is to make them repeatable and measurable. This means that daily tasks such as cleaning and sorting, storage, packing, labeling, and packaging are possible. Because workers know what they can expect, this helps them perform their jobs more efficiently.
Five steps are required to implement 5S: Sort, Set In Order, Standardize. Separate. Each step requires a different action, which increases efficiency. By sorting, for example, you make it easy to find the items later. When you arrange items, you place them together. Then, after you separate your inventory into groups, you store those groups in containers that are easy to access. Labeling your containers will ensure that everything is correctly labeled.
Employees will need to be more critical about their work. Employees should understand why they do the tasks they do, and then decide if there are better ways to accomplish them. To implement the 5S system, employees must acquire new skills and techniques.
In addition to improving efficiency, the 5S system also increases morale and teamwork among employees. They will feel motivated to strive for higher levels of efficiency once they start to see results.