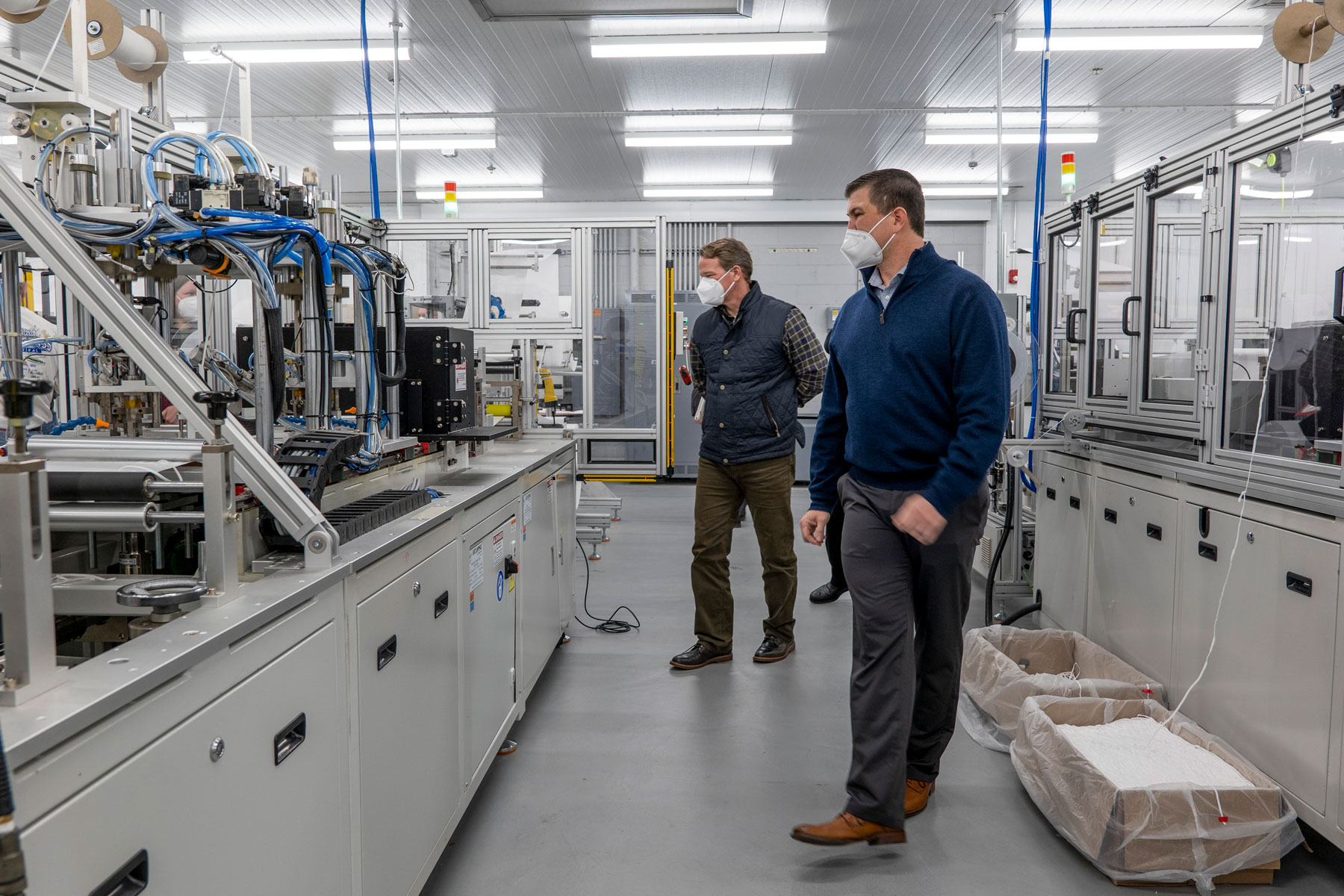
Creating a sustainable supply chain can be a challenge. Logistics of transport and packaging can make it difficult to reduce greenhouse gas emissions and create waste. Compact packaging can help reduce shipping costs and increase efficiency. Compact packaging can reduce waste and protect your bottom line.
Sustainability in supply chain requires a combination policy, processes, and technology. Many companies are constantly looking for new ways to reduce their carbon footprint, improve operational performance, and use sustainable materials. Many businesses offer training to suppliers to make them more sustainable.
A sustainable supply system can bring benefits to both the company's bottom line and the wider community. Companies can choose suppliers that use renewables and recycle materials. They can also reduce the number or offerings they make. They can also encourage suppliers who use sustainable material and establish a code to ensure the integrity of their suppliers.
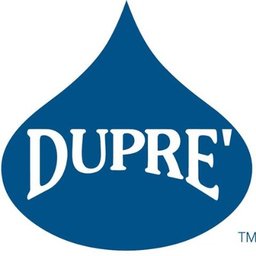
Companies can also reduce waste by remarketing returned products. They can also reduce the amount of water they use. Companies can set specific goals to improve their supply chain. They can also engage external and internal stakeholders to create change. They can also establish strong governance that will help them meet their sustainability targets.
Many companies are taking steps to reduce their emissions from facilities, purchased electricity, and transportation partners. However, many companies have yet not addressed indirect emissions caused by their supply chain partner. These include transportation and distribution partners. The Carbon Disclosure Project has reported that some companies have made progress in reducing greenhouse gas emissions, but there is still more work to be done.
To increase supply chain sustainability, companies must set clear goals, engage with internal and external stakeholders, measure performance, and establish quantifiable targets. They must also involve customers and suppliers to make sure they reach their goals. They must also make use of data to guide their decisions and set clear goals for the future.
Companies can also improve supply chain resilience by establishing robust risk management practices and by nearshoring or diversifying their suppliers. Bed Bath & Beyond is an example of a company that has established eight owned brands, and has increased control over its supply chain. It claims that at minimum half of its wood, cotton and other materials are sustainably sourced. It has also located key points for warehousing.
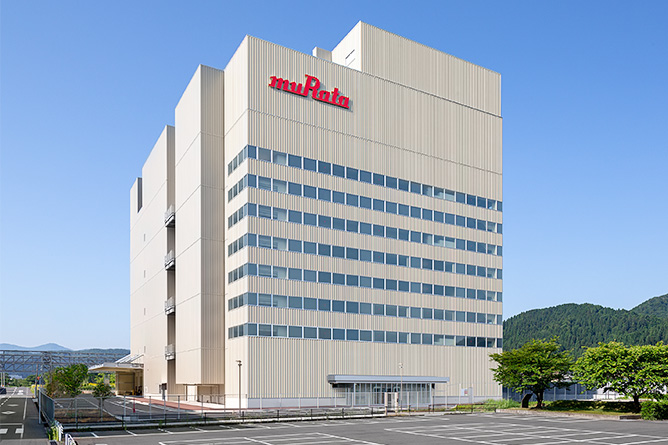
Companies must also consider the environmental impact of packaging. Some innovations may allow products to either be recycled or reused. These innovations also can help reduce the size of shipments, as well the number of trips they make. Also, companies have the option to invest in smaller packaging and upgrade their refrigeration equipment. These innovations can have long-lasting effects and they can reduce their carbon footprint.
Many companies are also adopting more circular economy models. They design products that can be reused and recycled, and they focus on the finite resources they have. This will help reduce greenhouse gas emissions and reduce waste.
FAQ
Why is logistics important in manufacturing?
Logistics are an essential part of any business. They enable you to achieve outstanding results by helping manage product flow from raw materials through to finished goods.
Logistics plays a significant role in reducing cost and increasing efficiency.
What are the four types in manufacturing?
Manufacturing is the process that transforms raw materials into useful products. Manufacturing can include many activities such as designing and building, testing, packaging shipping, selling, servicing, and other related activities.
What are the responsibilities for a manufacturing manager
Manufacturing managers must ensure that manufacturing processes are efficient, effective, and cost-effective. They should be aware of any issues within the company and respond accordingly.
They should also be able and comfortable communicating with other departments like sales and marketing.
They must also keep up-to-date with the latest trends in their field and be able use this information to improve productivity and efficiency.
How does a Production Planner differ from a Project Manager?
A production planner is more involved in the planning phase of the project than a project manger.
What is the responsibility of a production planner?
A production planner ensures all aspects of the project are delivered on time, within budget, and within scope. They also ensure the quality of the product and service meets the client's requirements.
What kind of jobs are there in logistics?
There are different kinds of jobs available in logistics. Here are some examples:
-
Warehouse workers - They load trucks and pallets.
-
Transportation drivers – They drive trucks or trailers to transport goods and perform pick-ups.
-
Freight handlers, - They sort out and pack freight in warehouses.
-
Inventory managers – They manage the inventory in warehouses.
-
Sales reps - They sell products and services to customers.
-
Logistics coordinators are responsible for organizing and planning logistics operations.
-
Purchasing agents - They buy goods and services that are necessary for company operations.
-
Customer service representatives - Answer calls and email from customers.
-
Shippers clerks - They process shipping order and issue bills.
-
Order fillers – They fill orders based upon what was ordered and shipped.
-
Quality control inspectors (QCI) - They inspect all incoming and departing products for potential defects.
-
Others – There are many other types available in logistics. They include transport supervisors, cargo specialists and others.
What are the 7 R's of logistics?
The acronym "7R's" of Logistics stands for seven principles that underpin logistics management. It was created by the International Association of Business Logisticians and published in 2004 under its "Seven Principles of Logistics Management".
The following letters form the acronym:
-
Responsive - ensure all actions are legal and not harmful to others.
-
Reliable: Have faith in your ability or the ability to honor any promises made.
-
It is reasonable to use resources efficiently and not waste them.
-
Realistic - consider all aspects of operations, including cost-effectiveness and environmental impact.
-
Respectful – Treat others fairly and equitably.
-
Resourceful - look for opportunities to save money and increase productivity.
-
Recognizable is a company that provides customers with value-added solutions.
Statistics
- You can multiply the result by 100 to get the total percent of monthly overhead. (investopedia.com)
- Job #1 is delivering the ordered product according to specifications: color, size, brand, and quantity. (netsuite.com)
- [54][55] These are the top 50 countries by the total value of manufacturing output in US dollars for its noted year according to World Bank.[56] (en.wikipedia.org)
- In 2021, an estimated 12.1 million Americans work in the manufacturing sector.6 (investopedia.com)
- In the United States, for example, manufacturing makes up 15% of the economic output. (twi-global.com)
External Links
How To
Six Sigma in Manufacturing
Six Sigma can be described as "the use of statistical process control (SPC), techniques to achieve continuous improvement." Motorola's Quality Improvement Department developed it at their Tokyo plant in Japan in 1986. Six Sigma's main goal is to improve process quality by standardizing processes and eliminating defects. This method has been adopted by many companies in recent years as they believe there are no perfect products or services. The main goal of Six Sigma is to reduce variation from the mean value of production. It is possible to measure the performance of your product against an average and find the percentage of time that it differs from the norm. If this deviation is too big, you know something needs fixing.
Understanding the dynamics of variability within your business is the first step in Six Sigma. Once you've understood that, you'll want to identify sources of variation. It is important to identify whether the variations are random or systemic. Random variations occur when people make mistakes; systematic ones are caused by factors outside the process itself. If you make widgets and some of them end up on the assembly line, then those are considered random variations. If however, you notice that each time you assemble a widget it falls apart in exactly the same spot, that is a problem.
After identifying the problem areas, you will need to devise solutions. This could mean changing your approach or redesigning the entire process. You should then test the changes again after they have been implemented. If they didn't work, then you'll need to go back to the drawing board and come up with another plan.