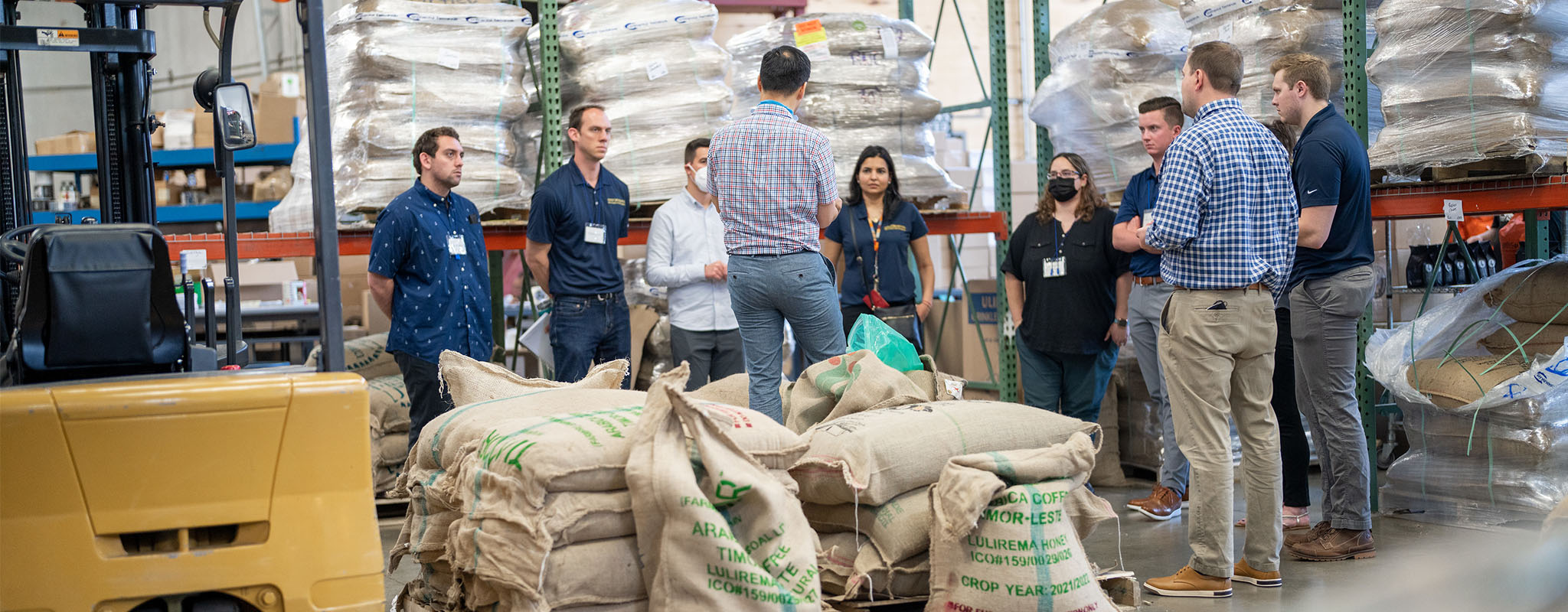
OEE stands for Overall Equipment Efficiency. This is a measure that can be used to evaluate the equipment's performance. This article will explain the basics of OEE and how it is calculated. It is a best practice indicator that is based upon Availability, Performance and Quality. OEE is used by manufacturers to increase production and reduce downtime. It is also a cost-saving tool for manufacturers.
OEE is a labor efficiency measure.
OEE can be used to measure overall production quality. It measures the interaction between availability, quality, performance. OEE is the time lost because of inconsistent production. These include the time down, rate fluctuations in process, scrap, and any rework that is generated during operative modes.
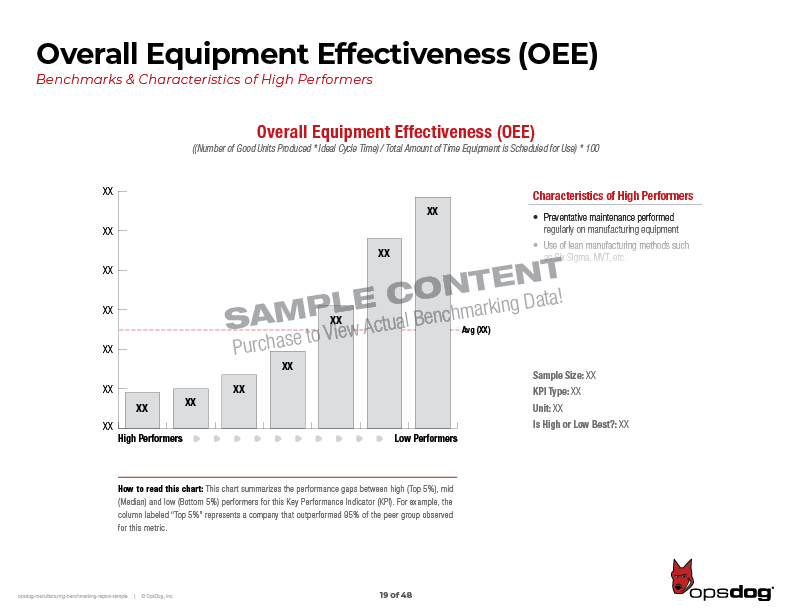
It is based Availability, Performance, Quality
OEE refers to a production management system that emphasizes availability, performance, and quality. The availability of a product/service is the period that it is available for sale. It could be the time between delivery to the customer and recovery or between scrapping and repair. Quality is directly linked to performance. It is possible to measure your performance by hiring a professional company who can evaluate your business processes and offer recommendations for improvement.
It is a benchmark for best practices.
OEE can be used to improve and measure your operation. This metric gives you different levels to analyze your operation, helping you to reduce waste and improve efficiency. It should be noted that this metric can not be used to determine the end all metric. You should pilot any OEE improvement program before you start it.
It is a directional metric
In addition to defining its exact definition, OEE is also a directional metric that is used to compare the performance of similar types of machines across a company. Companies can gauge if their machines have become more efficient by continuously measuring this metric across all of their machines.
It is a TPM metric
The overall equipment effectiveness (OEE) metric is a useful tool for analyzing production efficiency. It measures losses and inefficiencies across three key areas: availability; performance; and quality. It can also be used to track progress and identify areas where improvement is needed.
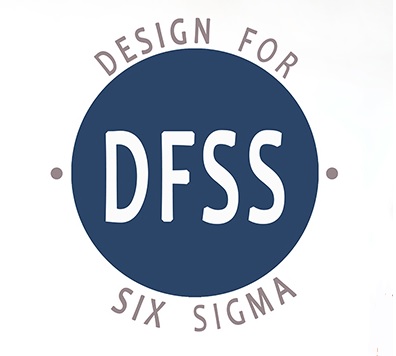
It is a best practice in manufacturing
OEE stands for overall equipment effectiveness. It's the ratio between how much a machine, cell or device can produce in a specific time and how long that product takes to actually be produced. It is important to minimize downtime and maximize OEE. Manufacturing operations can therefore improve quality and lower costs.
FAQ
What is it like to manage a logistics company?
It takes a lot of skills and knowledge to run a successful logistics business. Good communication skills are essential to effectively communicate with your suppliers and clients. It is important to be able to analyse data and draw conclusions. You must be able manage stress and pressure under pressure. To increase efficiency and creativity, you need to be creative. You must be a strong leader to motivate others and direct them to achieve organizational goals.
It is important to be organized and efficient in order to meet tight deadlines.
What is the responsibility for a logistics manager
Logistics managers make sure all goods are delivered on schedule and without damage. This is accomplished by using the experience and knowledge gained from working with company products. He/she must also ensure sufficient stock to meet the demand.
What is manufacturing and logistics?
Manufacturing refers to the process of making goods using raw materials and machines. Logistics encompasses the management of all aspects associated with supply chain activities such as procurement, production planning, distribution and inventory control. It also includes customer service. Logistics and manufacturing are often referred to as one thing. It encompasses both the creation of products and their delivery to customers.
What is the difference in Production Planning and Scheduling, you ask?
Production Planning (PP) is the process of determining what needs to be produced at any given point in time. Forecasting demand is one way to do this.
Scheduling involves the assignment of dates and times to tasks in order to complete them within the timeframe.
What is the responsibility of a production planner?
Production planners make sure that every aspect of the project is delivered on-time, within budget, and within schedule. They also ensure that the product/service meets the client’s needs.
What is the best way to learn about manufacturing?
You can learn the most about manufacturing by getting involved in it. If that is not possible, you could always read books or view educational videos.
Statistics
- According to a Statista study, U.S. businesses spent $1.63 trillion on logistics in 2019, moving goods from origin to end user through various supply chain network segments. (netsuite.com)
- In 2021, an estimated 12.1 million Americans work in the manufacturing sector.6 (investopedia.com)
- You can multiply the result by 100 to get the total percent of monthly overhead. (investopedia.com)
- Job #1 is delivering the ordered product according to specifications: color, size, brand, and quantity. (netsuite.com)
- Many factories witnessed a 30% increase in output due to the shift to electric motors. (en.wikipedia.org)
External Links
How To
How to use 5S in Manufacturing to Increase Productivity
5S stands to stand for "Sort", “Set In Order", “Standardize", and "Store". The 5S methodology was developed at Toyota Motor Corporation in 1954. It assists companies in improving their work environments and achieving higher efficiency.
This method aims to standardize production processes so that they are repeatable, measurable and predictable. This means that every day tasks such cleaning, sorting/storing, packing, and labeling can be performed. These actions allow workers to perform their job more efficiently, knowing what to expect.
Implementing 5S involves five steps: Sort, Set in Order, Standardize Separate, Store, and Each step requires a different action, which increases efficiency. If you sort items, it makes them easier to find later. You arrange items by placing them in an order. After you have divided your inventory into groups you can store them in easy-to-reach containers. You can also label your containers to ensure everything is properly labeled.
Employees will need to be more critical about their work. Employees need to be able understand their motivations and discover alternative ways to do them. To implement the 5S system, employees must acquire new skills and techniques.
The 5S Method not only improves efficiency, but it also helps employees to be more productive and happier. They feel more motivated to work towards achieving greater efficiency as they see the results.