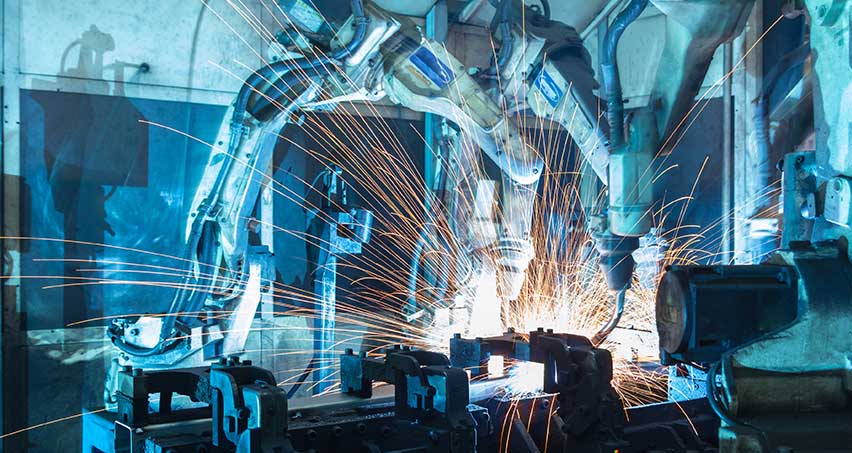
A supply chain manager should be skilled in managing manufacturing processes. This means they need to have a bachelor’s degree or higher and should have at most 10 years’ experience. They must also be able and willing to collaborate with other departments in the company. They must be self-motivated, and be able to make decisions that impact the supply chain. They should be knowledgeable in safety procedures as well as terminology and terms specific to the industry.
They oversee all aspects of logistics. They work closely with customers, suppliers, and other stakeholders to ensure the smooth running of the supply chain. They find solutions for any problem that may arise and help create an environment that is productive and functional. They are also responsible for coordinating the company's supply and distribution strategy.
They are responsible for managing the supply chain, which includes raw material procurement, production, distribution, and logistics. They should be able negotiate the prices of raw materials and equipment and be able monitor the effectiveness and efficiency of their supply chains. They must coordinate and plan transportation and storage routes and keep the company's inventory database current.
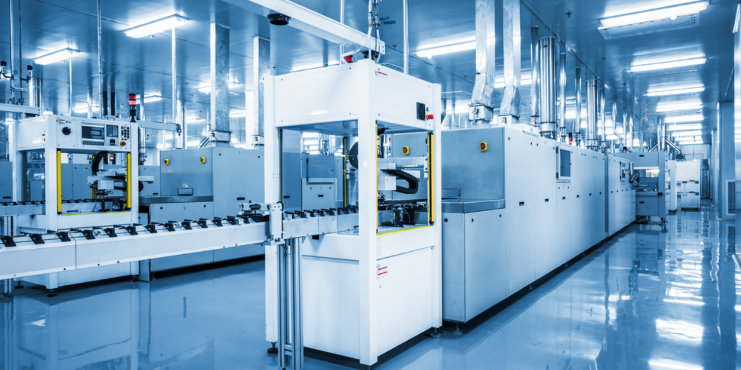
Supply chain managers are also responsible for ensuring that the company's products are of high quality. They also have to optimize the firm's financial and human capital. They are also responsible for identifying opportunities to recycle, reuse, and repurpose materials and products. They must also be able to anticipate needs throughout the production cycle.
Supply chain managers may work in a variety of industries, including automotive, fashion, food, and retail. They should be able and willing to communicate with all departments in their company. They should also be able to grasp supply chain management and management principles and strategies. They must also have a background in manufacturing, and they must be able to handle large-scale operations.
They must have specific training in supplier management and inventory control. They should be familiarized with the industry's policies. They should be able to organize systems and lead groups. They should also be able and willing to take charge of their team. They must have a good understanding and appreciation of the company's objectives and must be able and willing to communicate with suppliers.
Supply chain managers are also responsible for monitoring the environmental performance of their distribution partners. They may be required to look into the carbon footprints for their transport and storage providers. They will also need a keen eye on key performance indicators in the supply chain. They will need to find ways to reduce costs, such as shipping and delivery.
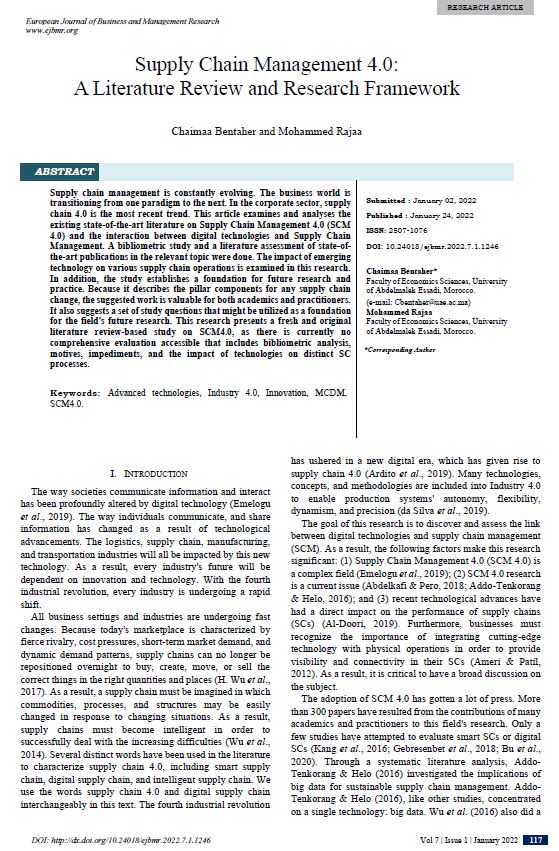
They are responsible for the coordination of work within their supply chain teams. They are also responsible to train new employees. They must have experience with transportation, purchasing, or manufacturing.
FAQ
What are the products of logistics?
Logistics refers to all activities that involve moving goods from A to B.
They cover all aspects of transportation, such as packing, loading, transporting and unloading.
Logisticians ensure that the right product reaches the right place at the right time and under safe conditions. They provide information on demand forecasts as well stock levels, production schedules and availability of raw material.
They can also track shipments in transit and monitor quality standards.
How can efficiency in manufacturing be improved?
The first step is to identify the most important factors affecting production time. The next step is to identify the most important factors that affect production time. If you don’t know where to begin, consider which factors have the largest impact on production times. Once you've identified them all, find solutions to each one.
How important is automation in manufacturing?
Not only are service providers and manufacturers important, but so is automation. They can provide services more quickly and efficiently thanks to automation. In addition, it helps them reduce costs by reducing human errors and improving productivity.
Statistics
- You can multiply the result by 100 to get the total percent of monthly overhead. (investopedia.com)
- According to the United Nations Industrial Development Organization (UNIDO), China is the top manufacturer worldwide by 2019 output, producing 28.7% of the total global manufacturing output, followed by the United States, Japan, Germany, and India.[52][53] (en.wikipedia.org)
- [54][55] These are the top 50 countries by the total value of manufacturing output in US dollars for its noted year according to World Bank.[56] (en.wikipedia.org)
- In 2021, an estimated 12.1 million Americans work in the manufacturing sector.6 (investopedia.com)
- (2:04) MTO is a production technique wherein products are customized according to customer specifications, and production only starts after an order is received. (oracle.com)
External Links
How To
How to Use the Just-In-Time Method in Production
Just-in-time is a way to cut costs and increase efficiency in business processes. It allows you to get the right amount resources at the right time. This means that you only pay the amount you actually use. The term was first coined by Frederick Taylor, who developed his theory while working as a foreman in the early 1900s. He observed how workers were paid overtime if there were delays in their work. He then concluded that if he could ensure that workers had enough time to do their job before starting to work, this would improve productivity.
JIT is a way to plan ahead and make sure you don't waste any money. The entire project should be looked at from start to finish. You need to ensure you have enough resources to tackle any issues that might arise. You'll be prepared to handle any potential problems if you know in advance. This will prevent you from spending extra money on unnecessary things.
There are several types of JIT techniques:
-
Demand-driven JIT: This is a JIT that allows you to regularly order the parts/materials necessary for your project. This will enable you to keep track of how much material is left after you use it. You'll also be able to estimate how long it will take to produce more.
-
Inventory-based: You stock materials in advance to make your projects easier. This allows you predict the amount you can expect to sell.
-
Project-driven: This method allows you to set aside enough funds for your project. You will be able to purchase the right amount of materials if you know what you need.
-
Resource-based JIT: This is the most popular form of JIT. You allocate resources based on the demand. For instance, if you have a lot of orders coming in, you'll assign more people to handle them. If you don't have many orders, you'll assign fewer people to handle the workload.
-
Cost-based: This approach is very similar to resource-based. However, you don't just care about the number of people you have; you also need to consider how much each person will cost.
-
Price-based: This approach is very similar to the cost-based method except that you don't look at individual workers costs but the total cost of the company.
-
Material-based: This is very similar to cost-based but instead of looking at total costs of the company you are concerned with how many raw materials you use on an average.
-
Time-based JIT: This is another variant of resource-based JIT. Instead of focusing on how much each employee costs, you focus on how long it takes to complete the project.
-
Quality-based JIT is another variant of resource-based JIT. Instead of looking at the labor costs and time it takes to make a product, think about its quality.
-
Value-based: This is one of the newest forms of JIT. This is where you don't care about how the products perform or whether they meet customers' expectations. Instead, you are focused on adding value to the marketplace.
-
Stock-based. This method is inventory-based and focuses only on the actual production at any given point. This method is useful when you want to increase production while decreasing inventory.
-
Just-in-time planning (JIT): This is a combination JIT and supply-chain management. It is the process of scheduling components' delivery as soon as they have been ordered. It's important because it reduces lead times and increases throughput.