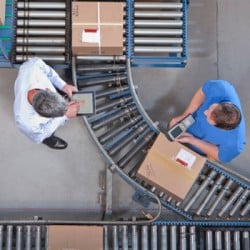
In the industrial manufacturing sector, there is increased global competition as well as a shortage skilled workers. In the 2020s, the industrial manufacturing industry is facing a challenging landscape. This is due to increased supply-chain volatility. To optimize growth in established markets as well as to identify growth opportunities, the Industrial Products & Services market requires a holistic culture of Innovation.
According to Deloitte and Manufacturing Institute, the US manufacturing sector will be experiencing the greatest shortage in skilled workers since the beginning of history. This is because 2 million jobs are unfilled over the next ten-years. As the industry prepares to face the future, manufacturers will need to decide how they will innovate and develop their digital capabilities. Deloitte's Industrial Manufacturing team can assist manufacturers in navigating the industry landscape.
The fourth industrial Revolution continues to disrupt the manufacturing sector. The industry must prepare its workforce to face a future that is based on networking within the 'internet of things,' and digital revolution. The Industrial Manufacturing team is experienced in establishing innovation management models that are grounded in industry-specific expertise and deep knowledge of the industry. It offers a broad range of digital transformation services that will help manufacturers succeed in a digitally disrupted world.
The Deloitte study is based on extensive secondary data analysis of labor supply, as well as interviews with executives from manufacturing organizations of all sizes. The research also includes economic projections. These findings highlight the importance and value of having a diverse workforce. Specifically, half of the respondents cited adaptability to company values as a key factor in their job satisfaction. Respondents also reported that more than one third believe employees must have a purpose for being satisfied at work. Executives also think that millennials value environmental awareness and are increasingly interested in climate change issues.
Deloitte projects that manufacturing GDP growth will be moderate at 1.3 percent by 2020, based on the Oxford Economic Model. However, the study indicates that this rate of growth is likely to be less than half what it was in the past few year. This will force companies to rethink their supply chain assurance strategies. In addition to this, companies must focus on larger management initiatives, such increasing resilience in operations. According to Deloitte's study, manufacturers will be making decisions regarding work environments and work practices.
In order to prepare for the future, manufacturing companies need to develop pathways for careers and develop an inclusive culture. It is possible to improve manufacturing efficiency by increasing resilience and reduce waste. Combining digital technologies with lean principles can help to reduce manufacturing variability.
Deloitte releases a new report about diversity in manufacturing, as the US manufacturing sector continues to develop. Deloitte’s Beyond Reskilling report discusses diversity and how it is vital for the future of manufacturing. It also highlights benefits of having a diverse workforce.
FAQ
What are manufacturing & logistics?
Manufacturing refers the process of producing goods from raw materials through machines and processes. Logistics includes all aspects related to supply chain management, such as procurement, distribution planning, inventory control and transportation. Manufacturing and logistics can often be grouped together to describe a larger term that covers both the creation of products, and the delivery of them to customers.
How can manufacturing reduce production bottlenecks?
You can avoid bottlenecks in production by making sure that everything runs smoothly throughout the production cycle, from the moment you receive an order to the moment the product is shipped.
This includes both quality control and capacity planning.
Continuous improvement techniques like Six Sigma are the best way to achieve this.
Six Sigma management is a system that improves quality and reduces waste within your organization.
It focuses on eliminating variation and creating consistency in your work.
What are the differences between these four types?
Manufacturing refers the process of turning raw materials into useful products with machines and processes. It can involve many activities like designing, manufacturing, testing packaging, shipping, selling and servicing.
Can we automate some parts of manufacturing?
Yes! Automation has been around since ancient times. The Egyptians invent the wheel thousands of year ago. Nowadays, we use robots for assembly lines.
There are many uses of robotics today in manufacturing. These include:
-
Robots for assembly line
-
Robot welding
-
Robot painting
-
Robotics inspection
-
Robots create products
Automation can be applied to manufacturing in many other ways. 3D printing, for example, allows us to create custom products without waiting for them to be made.
What is the difference in Production Planning and Scheduling, you ask?
Production Planning (PP) is the process of determining what needs to be produced at any given point in time. This can be done by forecasting demand and identifying production capabilities.
Scheduling refers the process by which tasks are assigned dates so that they can all be completed within the given timeframe.
What skills should a production planner have?
Production planners must be flexible, organized, and able handle multiple tasks. Effective communication with clients and colleagues is essential.
What does warehouse mean?
A warehouse is a place where goods are stored until they are sold. It can be indoors or out. In some cases it could be both indoors and outdoors.
Statistics
- In 2021, an estimated 12.1 million Americans work in the manufacturing sector.6 (investopedia.com)
- In the United States, for example, manufacturing makes up 15% of the economic output. (twi-global.com)
- It's estimated that 10.8% of the U.S. GDP in 2020 was contributed to manufacturing. (investopedia.com)
- According to a Statista study, U.S. businesses spent $1.63 trillion on logistics in 2019, moving goods from origin to end user through various supply chain network segments. (netsuite.com)
- (2:04) MTO is a production technique wherein products are customized according to customer specifications, and production only starts after an order is received. (oracle.com)
External Links
How To
How to Use Just-In-Time Production
Just-in-time is a way to cut costs and increase efficiency in business processes. It's a way to ensure that you get the right resources at just the right time. This means that you only pay for what you actually use. The term was first coined by Frederick Taylor, who developed his theory while working as a foreman in the early 1900s. He noticed that workers were often paid overtime when they had to work late. He decided that workers would be more productive if they had enough time to complete their work before they started to work.
JIT is a way to plan ahead and make sure you don't waste any money. You should also look at the entire project from start to finish and make sure that you have sufficient resources available to deal with any problems that arise during the course of your project. If you expect problems to arise, you will be able to provide the necessary equipment and personnel to address them. This will ensure that you don't spend more money on things that aren't necessary.
There are many JIT methods.
-
Demand-driven JIT: You order the parts and materials you need for your project every other day. This will enable you to keep track of how much material is left after you use it. This will allow to you estimate the time it will take for more to be produced.
-
Inventory-based: This is a type where you stock the materials required for your projects in advance. This allows you to forecast how much you will sell.
-
Project-driven: This approach involves setting aside sufficient funds to cover your project's costs. Knowing how much money you have available will help you purchase the correct amount of materials.
-
Resource-based JIT: This type of JIT is most commonly used. You allocate resources based on the demand. If you have many orders, you will assign more people to manage them. If there aren't many orders, you will assign fewer people.
-
Cost-based: This is a similar approach to resource-based but you are not only concerned with how many people you have, but also how much each one costs.
-
Price-based: This approach is very similar to the cost-based method except that you don't look at individual workers costs but the total cost of the company.
-
Material-based: This is very similar to cost-based but instead of looking at total costs of the company you are concerned with how many raw materials you use on an average.
-
Time-based: This is another variation of resource-based JIT. Instead of focusing on how much each employee costs, you focus on how long it takes to complete the project.
-
Quality-based JIT: Another variation on resource-based JIT. Instead of worrying about the costs of each employee or how long it takes for something to be made, you should think about how quality your product is.
-
Value-based JIT: This is the latest form of JIT. You don't worry about whether the products work or if they meet customer expectations. Instead, you focus on the added value that you provide to your market.
-
Stock-based. This method is inventory-based and focuses only on the actual production at any given point. It's used when you want to maximize production while minimizing inventory.
-
Just-intime (JIT), planning is a combination JIT management and supply chain management. It's the process of scheduling delivery of components immediately after they are ordered. It's important as it reduces leadtimes and increases throughput.