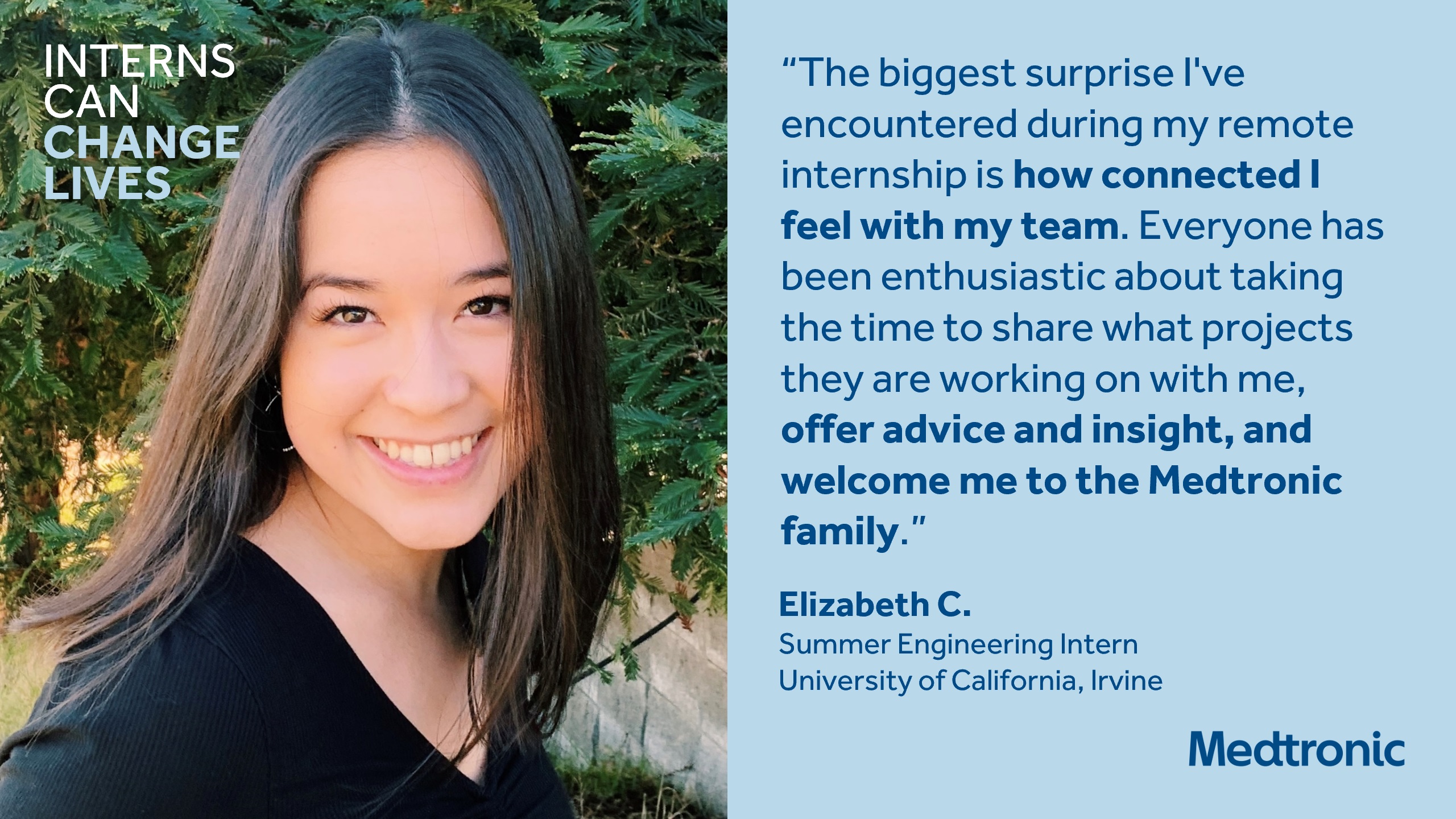
A nuclear engineer can earn anywhere between six figures and seven figures. Neben their regular duties, a nuclear engineer may also be responsible for overseeing the construction and operation of closed facilities. They may have to defend their work in public. Nuclear engineers are in demand for a wide variety of reasons. They are highly sought after for their leadership abilities and technical expertise. There are many factors that affect the salary of this profession, such as education and experience.
A bachelor's degree is enough to earn a salary as a nuclear engineer.
The federal government is the biggest employer of nuclear engineers. Other prominent employers include the engineering and scientific research and design services sectors. A growing interest and demand for nuclear engineering professionals is expected to drive up the demand in the engineering, research and development and manufacturing sectors over the next decade. Although there aren't many commercial nuclear power stations currently operating, the new technology could help increase their production.
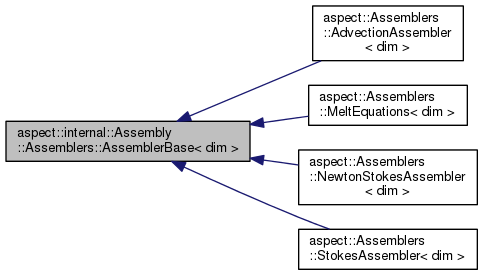
In order to become a nuclear engineer, you must have a bachelor's degree in engineering or a related field. A bachelor's program in nuclear engineering may lead to entry-level jobs or a better career path after you have completed a masters program. Some positions require state licensure. For their first few year, nuclear engineers usually work under an experienced engineer. They gain experience and take responsibility.
Average salary for nuclear engineers with master's degrees
Consider the salaries for nuclear engineers if your career is in this field. While you can find a job at any nuclear power plant, it is common to work in an office setting. The majority of people interested in a career working in nuclear energy will work in power stations and work with mechanical and electrical engineers. These professionals will help them integrate systems they have designed. Nuclear engineers are typically full-time workers and may even work more than their counterparts.
A nuclear engineer with a Master of Science degree will earn $124 27,272 annually, which is significantly more that the average wage for all US workers. It is important to remember that salaries vary from one position to the next. An average salary for nuclear engineers is $185,550. The average starting salary for nuclear engineers is $74,800. This is one of the highest salaries in the field.
The starting salary of a nuclear engineering engineer
If you're considering a career in nuclear engineering, you'll want to know how much the average starting salary is. You need to have a strong education and a lot of work experience. Nuclear engineers can expect steady career growth. However, they are also able to move into a similar field if needed. Nuclear engineers may also be involved in space exploration, manufacturing, and medical uses of radiological substances.
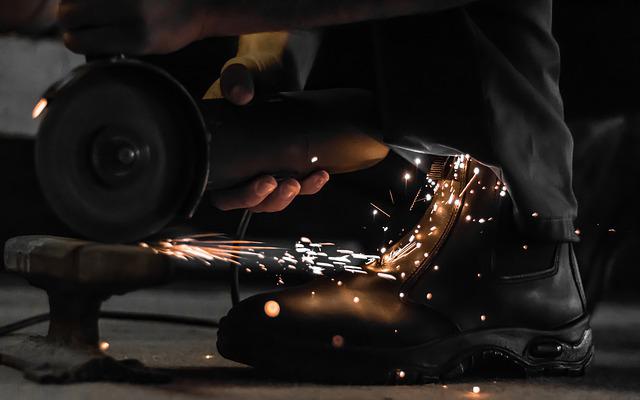
Nuclear engineers can work in many industries but the federal government is their largest employer. The Office for Nuclear Regulation oversees the operations of these facilities. Other industries that are available to this profession include construction, manufacturing and scientific research, as well as scientific research, development, and other technical services. Nuclear engineers can expect to find more employment opportunities as the use of nuclear energy increases. However, graduates with this degree will likely not have the best job prospects. Currently, the federal government has limited jobs for nuclear engineers, but there are a number of companies that are hiring for these professionals.
FAQ
What does manufacturing industry mean?
Manufacturing Industries are those businesses that make products for sale. Consumers are those who purchase these products. These companies use various processes such as production, distribution, retailing, management, etc., to fulfill this purpose. They produce goods from raw materials by using machines and other machinery. This includes all types manufactured goods such as clothing, building materials, furniture, electronics, tools and machinery.
How can manufacturing excess production be decreased?
The key to reducing overproduction lies in developing better ways to manage inventory. This would reduce time spent on activities such as purchasing, stocking, and maintaining excess stock. By doing this, we could free up resources for other productive tasks.
You can do this by adopting a Kanban method. A Kanban Board is a visual display that tracks work progress. A Kanban system allows work items to move through several states before reaching their final destination. Each state represents a different priority.
To illustrate, work can move from one stage or another when it is complete enough for it to be moved to a new stage. However, if a task is still at the beginning stages, it will remain so until it reaches the end of the process.
This allows you to keep work moving along while making sure that no work gets neglected. A Kanban board allows managers to monitor how much work is being completed at any given moment. This allows them the ability to adjust their workflow using real-time data.
Lean manufacturing, another method to control inventory levels, is also an option. Lean manufacturing seeks to eliminate waste from every step of the production cycle. Anything that does not contribute to the product's value is considered waste. There are several types of waste that you might encounter:
-
Overproduction
-
Inventory
-
Unnecessary packaging
-
Materials in excess
These ideas can help manufacturers improve efficiency and reduce costs.
What is the difference between a production planner and a project manager?
The primary difference between a producer planner and a manager of a project is that the manager usually plans and organizes the whole project, while a production planner is only involved in the planning stage.
How can manufacturing efficiency improved?
The first step is to determine the key factors that impact production time. We must then find ways that we can improve these factors. If you don't know where to start, then think about which factor(s) have the biggest impact on production time. Once you have identified the factors, then try to find solutions.
Statistics
- (2:04) MTO is a production technique wherein products are customized according to customer specifications, and production only starts after an order is received. (oracle.com)
- In the United States, for example, manufacturing makes up 15% of the economic output. (twi-global.com)
- You can multiply the result by 100 to get the total percent of monthly overhead. (investopedia.com)
- According to the United Nations Industrial Development Organization (UNIDO), China is the top manufacturer worldwide by 2019 output, producing 28.7% of the total global manufacturing output, followed by the United States, Japan, Germany, and India.[52][53] (en.wikipedia.org)
- In 2021, an estimated 12.1 million Americans work in the manufacturing sector.6 (investopedia.com)
External Links
How To
How to use 5S to increase Productivity in Manufacturing
5S stands for "Sort", 'Set In Order", 'Standardize', & Separate>. The 5S methodology was developed at Toyota Motor Corporation in 1954. It allows companies to improve their work environment, thereby achieving greater efficiency.
This method has the basic goal of standardizing production processes to make them repeatable. It means tasks like cleaning, sorting or packing, labeling, and storing are done every day. Workers can be more productive by knowing what to expect.
Implementing 5S requires five steps. These are Sort, Set In Order, Standardize. Separate. And Store. Each step involves a different action which leads to increased efficiency. By sorting, for example, you make it easy to find the items later. When items are ordered, they are put together. You then organize your inventory in groups. Finally, label all containers correctly.
This requires employees to critically evaluate how they work. Employees must understand why they do certain tasks and decide if there's another way to accomplish them without relying on the old ways of doing things. In order to use the 5S system effectively, they must be able to learn new skills.
The 5S method increases efficiency and morale among employees. They will feel motivated to strive for higher levels of efficiency once they start to see results.