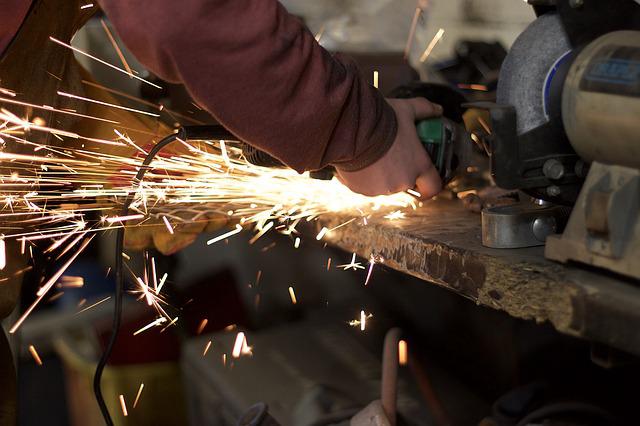
Hoshin Kanri and Value Stream Mapping are some of the lean tools. These methods combine statistical data with quality control measures to improve process performance and reduce defects. Lean tools can also improve safety and health, cycle time and delivery time, as well as quality and raw material. Check out our articles about lean tools for more information. We provide examples and explain some of the basics.
Hoshin Kari
It is crucial that each department communicates the goals to the other when implementing Hoshin Kanri's principles. It's important to clearly communicate your company’s objectives and the results you get. You can view a sample Hoshin Kanri matrix by searching Google Images. The basic idea behind the matrix is that you want everyone to be aligned towards the same goals so everyone can work towards them.
Hoshin Kanri, an inclusive method, can help you identify which aspects of your company need to be improved. This method can help you to identify the activities that need to be improved and to establish a clear pathway from general goals towards concrete actions. You can use this tool to measure your progress and show how each step is related to the others. Hoshin Kanri believes in a collaborative approach to improving the company's overall performance.
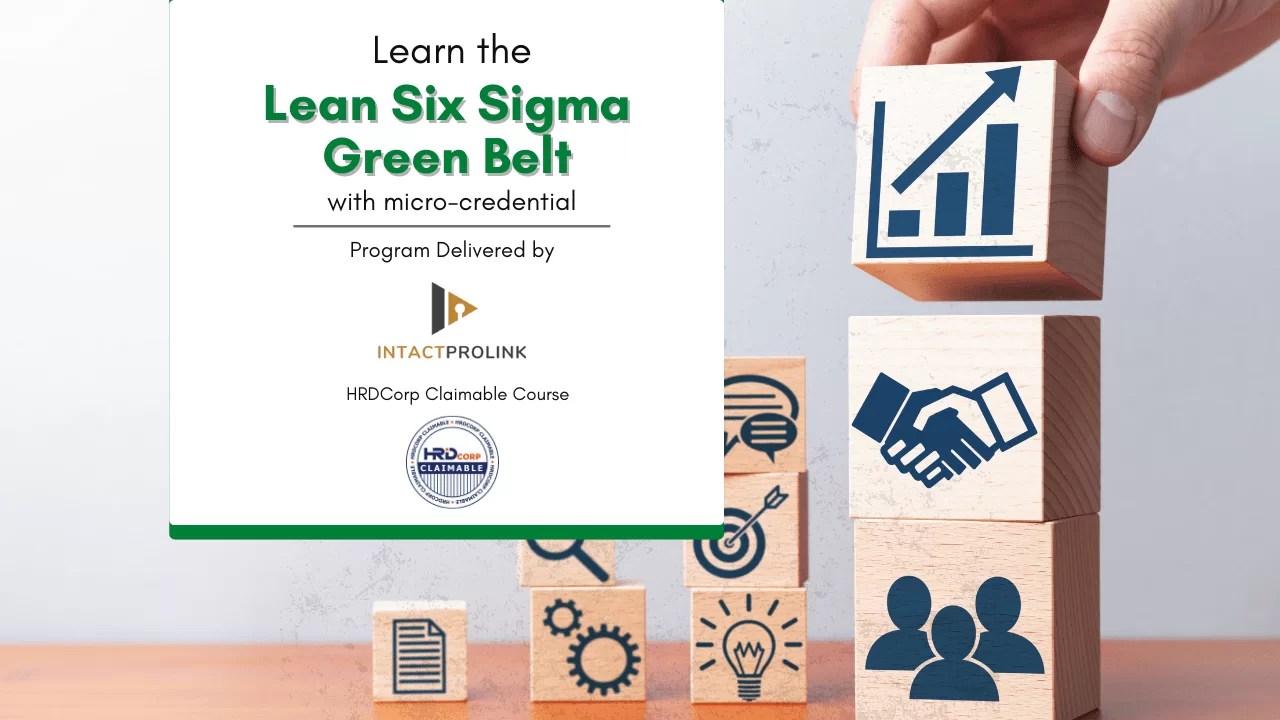
Visual board
The visual board is powerful in measuring the outcomes of a process but not an all-purpose tool. It cannot be used to implement a process that involves people. The visual management board should be personalized for the user to bring out emotion behind the numbers. It can also be a tool for tracking performance indicators like pieces produced per standard time or labor hours. Although there is not a universal code, there are key elements that make this tool useful in lean production environments.
One of the key aspects of a visual management board is the ability to quickly communicate to all members of a team what needs to be done and who is responsible for each task. The board can display this information in less than 20 seconds. To ensure that everyone on the same page, managers must also see results from these activities. To ensure everyone is on the same page, a visual management board can easily be created and updated.
Value Stream Mapping
A facilitator should identify the bottleneck in order to use value stream mapping in tools Lean. A bottleneck refers to the process step that has the largest WIP. For example, suppose a three-step process has 60 units per an hour throughput but a potential total WIP of 42 units, Step 2 is the bottleneck. A value stream map can help identify bottlenecks and find process improvements.
Understanding the customer perspective and the system or process is key to a successful value stream mapping. This is a complex and cross-functional process. This may require extensive involvement and training. Larger companies might hire a value stream manager to lead the mapping. Although value stream mapping may be a big project, smaller projects can identify areas where there are potential savings and improvements. A powerful tool in tools Lean is value stream mapping.
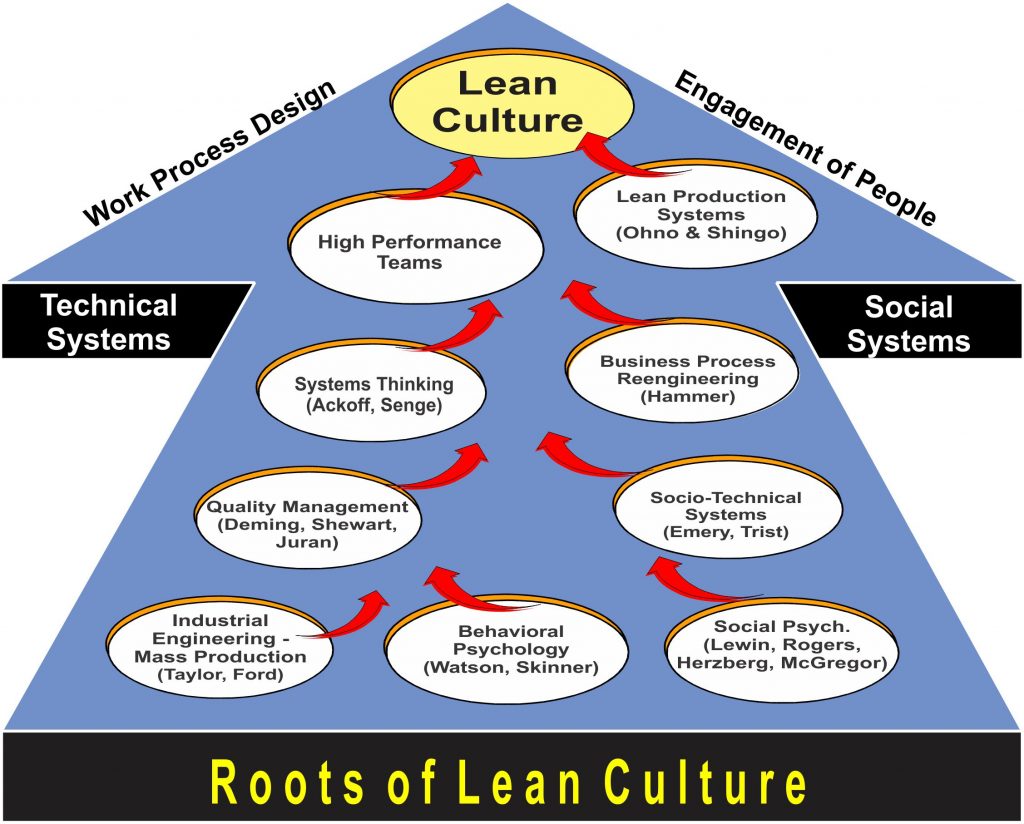
Process Observation and Analysis
Lean management relies on continuous improvement and process monitoring. Process observation is used to verify that standards are being met and that processes are producing the desired results. In the end, abandoned processes will become less efficient. Process observation and analysis may have cultural implications. Managers should clearly communicate the reasons for process observation and the potential benefits. Process observation and analysis is a fundamental part of the lean management system, so managers must communicate why it's important to them and their team.
When implementing Lean, the first step is to verify the process flow map by conducting a walk-through of the process. After this step has been completed, it is time to analyze the data collected. The Measure phase involves gathering data on the current product, process, or service. The project leader uses statistical hypothesis testing techniques to identify the root cause of the problem. Analyses determine whether the problem can be eliminated or solved.
FAQ
What are the 7 Rs of logistics?
The acronym 7R's for Logistics stands to represent the seven basic principles in logistics management. It was developed by International Association of Business Logisticians (IABL), and published as part of their "Seven Principles of Logistics Management Series" in 2004.
The following letters make up the acronym:
-
Responsible - to ensure that all actions are within the legal requirements and are not detrimental to others.
-
Reliable - You can have confidence that you will fulfill your promises.
-
Reasonable - make sure you use your resources well and don't waste them.
-
Realistic – consider all aspects of operations, from cost-effectiveness to environmental impact.
-
Respectful – Treat others fairly and equitably.
-
Resourceful - look for opportunities to save money and increase productivity.
-
Recognizable: Provide customers with value-added service
How can manufacturing overproduction be reduced?
In order to reduce excess production, you need to develop better inventory management methods. This would reduce the time needed to manage inventory. This could help us free up our time for other productive tasks.
One way to do this is to adopt a Kanban system. A Kanban board is a visual display used to track work in progress. Kanban systems are where work items travel through a series of states until reaching their final destination. Each state represents a different priority level.
For instance, when work moves from one stage to another, the current task is complete enough to be moved to the next stage. But if a task remains in the beginning stages it will stay that way until it reaches its end.
This allows you to keep work moving along while making sure that no work gets neglected. A Kanban board allows managers to monitor how much work is being completed at any given moment. This information allows managers to adjust their workflow based off real-time data.
Lean manufacturing, another method to control inventory levels, is also an option. Lean manufacturing works to eliminate waste throughout every stage of the production chain. Anything that doesn't add value to the product is considered waste. There are several types of waste that you might encounter:
-
Overproduction
-
Inventory
-
Packaging that is not necessary
-
Materials in excess
Manufacturers can reduce their costs and improve their efficiency by using these ideas.
Why automate your warehouse
Automation has become increasingly important in modern warehousing. E-commerce has increased the demand for quicker delivery times and more efficient processes.
Warehouses must be able to quickly adapt to changing demands. In order to do this, they need to invest in technology. Automating warehouses has many benefits. Here are some of the reasons automation is worth your investment:
-
Increases throughput/productivity
-
Reduces errors
-
Increases accuracy
-
Safety increases
-
Eliminates bottlenecks
-
Companies can scale more easily
-
This makes workers more productive
-
Gives you visibility into all that is happening in your warehouse
-
Enhances customer experience
-
Improves employee satisfaction
-
This reduces downtime while increasing uptime
-
This ensures that quality products are delivered promptly
-
Human error can be eliminated
-
This helps to ensure compliance with regulations
Statistics
- You can multiply the result by 100 to get the total percent of monthly overhead. (investopedia.com)
- Many factories witnessed a 30% increase in output due to the shift to electric motors. (en.wikipedia.org)
- It's estimated that 10.8% of the U.S. GDP in 2020 was contributed to manufacturing. (investopedia.com)
- According to the United Nations Industrial Development Organization (UNIDO), China is the top manufacturer worldwide by 2019 output, producing 28.7% of the total global manufacturing output, followed by the United States, Japan, Germany, and India.[52][53] (en.wikipedia.org)
- [54][55] These are the top 50 countries by the total value of manufacturing output in US dollars for its noted year according to World Bank.[56] (en.wikipedia.org)
External Links
How To
How to use the Just-In Time Method in Production
Just-in time (JIT), is a process that reduces costs and increases efficiency in business operations. It allows you to get the right amount resources at the right time. This means that you only pay the amount you actually use. Frederick Taylor, a 1900s foreman, first coined the term. He noticed that workers were often paid overtime when they had to work late. He decided to ensure workers have enough time to do their jobs before starting work to improve productivity.
JIT is a way to plan ahead and make sure you don't waste any money. Also, you should look at the whole project from start-to-finish and make sure you have the resources necessary to address any issues. If you anticipate that there might be problems, you'll have enough people and equipment to fix them. You won't have to pay more for unnecessary items.
There are several types of JIT techniques:
-
Demand-driven JIT: You order the parts and materials you need for your project every other day. This will let you track the amount of material left over after you've used it. This will allow to you estimate the time it will take for more to be produced.
-
Inventory-based: You stock materials in advance to make your projects easier. This allows you to forecast how much you will sell.
-
Project-driven: This approach involves setting aside sufficient funds to cover your project's costs. Knowing how much money you have available will help you purchase the correct amount of materials.
-
Resource-based JIT is the most widespread form. You allocate resources based on the demand. You will, for example, assign more staff to deal with large orders. If you don’t have many orders you will assign less people to the work.
-
Cost-based: This is similar to resource-based, except that here you're not just concerned about how many people you have but how much each person costs.
-
Price-based: This is very similar to cost-based, except that instead of looking at how much each individual worker costs, you look at the overall price of the company.
-
Material-based: This is very similar to cost-based but instead of looking at total costs of the company you are concerned with how many raw materials you use on an average.
-
Time-based: Another variation of resource-based JIT. Instead of worrying about how much each worker costs, you can focus on how long the project takes.
-
Quality-based JIT: This is another variation of resource based JIT. Instead of thinking about how much each employee costs or how long it takes to manufacture something, you think about how good the quality of your product is.
-
Value-based JIT: This is the latest form of JIT. In this instance, you are not concerned about the product's performance or meeting customer expectations. Instead, you are focused on adding value to the marketplace.
-
Stock-based. This method is inventory-based and focuses only on the actual production at any given point. This is used to increase production and minimize inventory.
-
Just-in time (JIT), planning: This is a combination JIT/supply chain management. It's the process of scheduling delivery of components immediately after they are ordered. It's important as it reduces leadtimes and increases throughput.