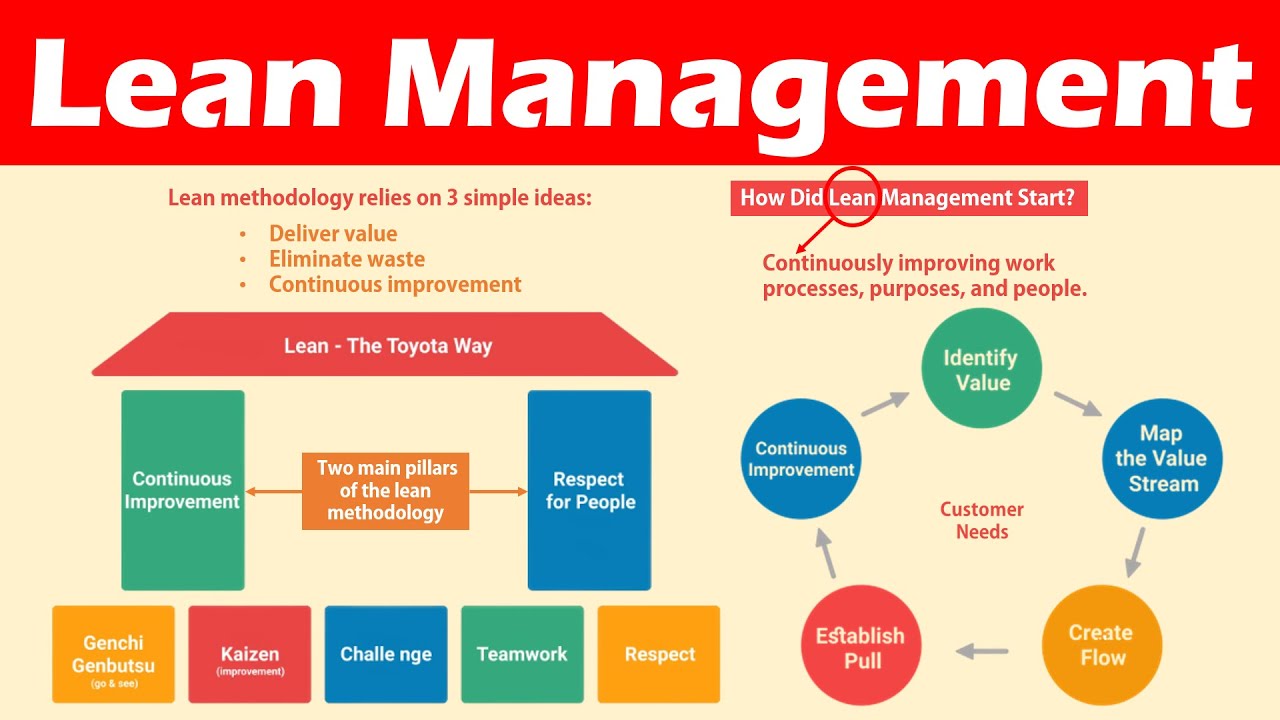
It is important to include the core qualifications section in your job description for environmental engineer. To ensure a competitive pool, you will need to outline the minimum requirements for the job. This will help you avoid applying for jobs that aren't qualified. To make sure that the hiring process is as smooth as possible, a skills section is a great idea. Read on for more. To stand out among others, this job description must be written in a formal, professional style.
Qualifications
You might be considering changing careers to environmental engineering. Here are some details. The job involves the development and implementation of systems that control air and water quality and site remediation. This position often requires collaboration with other professionals, such as environmental specialists and hazardous waste technicians. Environmental engineers are often called upon to provide technical assistance in environmental litigation and remediation projects. They monitor progress of environmental improvement projects and help to develop environmental journals.
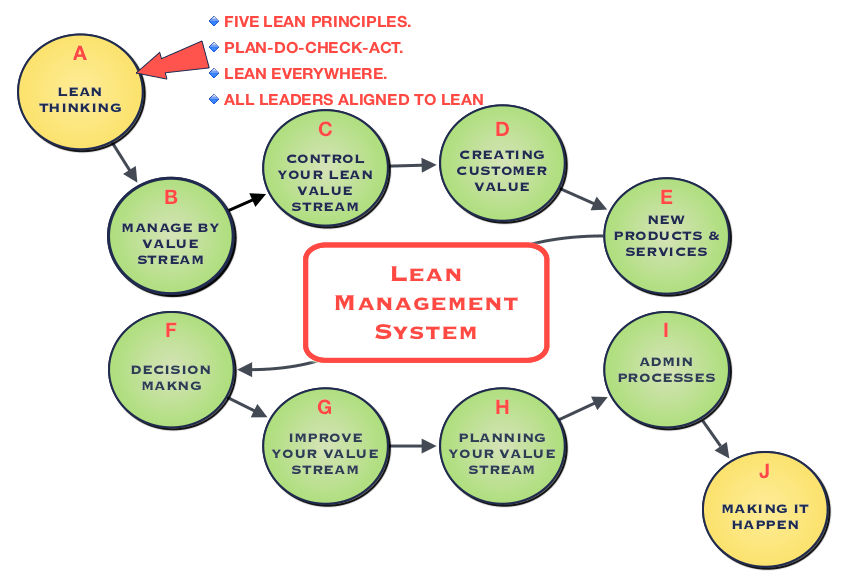
A role as an environmental engineer requires extensive field and office work. An environmental engineer may be responsible for field inspections, characterizing and evaluating materials, or working with subcontractors on site. It is also necessary to have a thorough understanding of environmental regulations. In addition, they may be required to create and maintain spreadsheets and other elements of a report. They may be involved in many different projects and they can move from their related fields to their own.
Responsibilities
A variety of responsibilities are available to an environmental engineer. Engineers may develop technologies to manage pollution or make recommendations about clean-up procedures. They may also work with legal counsel and other experts, such as those in the fields of law and business. Administrative duties include preparing reports and spreadsheets, as well as the preparation of reports. Environmental engineers may advise federal, regional, and local government agencies in matters of environmental protection.
An environmental engineer also has the responsibility of assisting with the creation and implementation of plans and programs to conserve and manage natural resources. They are responsible for assessing the impacts of any proposed commercial activity on land or other resources. They are responsible for general administrative tasks including preparing project documentation, training staff, as well as budget implementation. An environmental engineer may also advise policymakers on environmental issues and best practices.
Future employment outlook
The employment outlook is favorable for environmental engineers. Engineers can assist companies in complying with environmental regulations, developing alternative methods to reduce pollution and managing the waste they produce. There is a strong demand. Environmental engineers will see a rise in demand due to the growing population and emphasis on prevention. As workers leave and move into other fields or retire, job opportunities will increase. This job is not for everyone. These are some of the jobs that you could apply for in future.
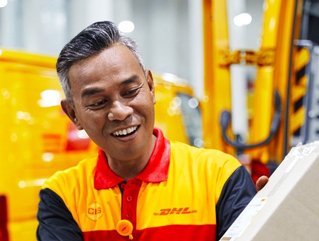
Most environmental engineers work in offices or laboratories. Some work indoors while others travel or spend time outside. They typically work forty hours a week. Your schedule might vary for certain jobs that require you to travel. The work can be demanding, especially if deadlines are involved. Environmental engineers should be aware of their physical limitations, as the environment is their primary concern. This occupation is often subject to high levels of stress and long working hours.
FAQ
What is the difference between Production Planning, Scheduling and Production Planning?
Production Planning (PP), also known as forecasting and identifying production capacities, is the process that determines what product needs to be produced at any particular time. This is accomplished by forecasting the demand and identifying production resources.
Scheduling is the process of assigning specific dates to tasks so they can be completed within the specified timeframe.
What are the products and services of logistics?
Logistics involves the transportation of goods from point A and point B.
They cover all aspects of transportation, such as packing, loading, transporting and unloading.
Logisticians ensure that the right product reaches the right place at the right time and under safe conditions. They provide information on demand forecasts as well stock levels, production schedules and availability of raw material.
They monitor shipments in transit, ensure quality standards, manage inventories, replenish orders, coordinate with suppliers and other vendors, and offer support services for sales, marketing, and customer service.
Is there anything we should know about Manufacturing Processes prior to learning about Logistics.
No. It doesn't matter if you don't know anything about manufacturing before you learn about logistics. Knowing about manufacturing processes will help you understand how logistics works.
What is the responsibility for a logistics manager
Logistics managers are responsible for ensuring that all goods arrive in perfect condition and on time. This is done by using his/her experience and knowledge of the company's products. He/she should also ensure enough stock is available to meet demand.
Is automation important in manufacturing?
Not only is automation important for manufacturers, but it's also vital for service providers. It allows them provide faster and more efficient services. It helps them to lower costs by reducing human errors, and improving productivity.
What is the role of a production manager?
A production planner makes sure all project elements are delivered on schedule, within budget, as well as within the agreed scope. They ensure that the product or service is of high quality and meets client requirements.
What is the best way to learn about manufacturing?
Hands-on experience is the best way to learn more about manufacturing. If that is not possible, you could always read books or view educational videos.
Statistics
- In the United States, for example, manufacturing makes up 15% of the economic output. (twi-global.com)
- You can multiply the result by 100 to get the total percent of monthly overhead. (investopedia.com)
- In 2021, an estimated 12.1 million Americans work in the manufacturing sector.6 (investopedia.com)
- (2:04) MTO is a production technique wherein products are customized according to customer specifications, and production only starts after an order is received. (oracle.com)
- Job #1 is delivering the ordered product according to specifications: color, size, brand, and quantity. (netsuite.com)
External Links
How To
How to use lean manufacturing in the production of goods
Lean manufacturing (or lean manufacturing) is a style of management that aims to increase efficiency, reduce waste and improve performance through continuous improvement. It was first developed in Japan in the 1970s/80s by Taiichi Ahno, who was awarded the Toyota Production System (TPS), award from KanjiToyoda, the founder of TPS. Michael L. Watkins published the "The Machine That Changed the World", the first book about lean manufacturing. It was published in 1990.
Lean manufacturing refers to a set of principles that improve the quality, speed and costs of products and services. It emphasizes the elimination of defects and waste throughout the value stream. Lean manufacturing is called just-in-time (JIT), zero defect, total productive maintenance (TPM), or 5S. Lean manufacturing is about eliminating activities that do not add value, such as inspection, rework, and waiting.
Lean manufacturing can help companies improve their product quality and reduce costs. Additionally, it helps them achieve their goals more quickly and reduces employee turnover. Lean manufacturing is considered one of the most effective ways to manage the entire value chain, including suppliers, customers, distributors, retailers, and employees. Lean manufacturing can be found in many industries. For example, Toyota's philosophy underpins its success in automobiles, electronics, appliances, healthcare, chemical engineering, aerospace, paper, food, etc.
Lean manufacturing includes five basic principles:
-
Define Value: Identify the social value of your business and what sets you apart.
-
Reduce waste - Get rid of any activity that does not add value to the supply chain.
-
Create Flow - Ensure work moves smoothly through the process without interruption.
-
Standardize & Simplify - Make processes as consistent and repeatable as possible.
-
Build Relationships- Develop personal relationships with both internal as well as external stakeholders.
Lean manufacturing is not a new concept, but it has been gaining popularity over the last few years due to a renewed interest in the economy following the global financial crisis of 2008. To increase their competitiveness, many businesses have turned to lean manufacturing. In fact, some economists believe that lean manufacturing will be an important factor in economic recovery.
With many benefits, lean manufacturing is becoming more common in the automotive industry. These include improved customer satisfaction, reduced inventory levels, lower operating costs, increased productivity, and better overall safety.
You can apply Lean Manufacturing to virtually any aspect of your organization. This is because it ensures efficiency and effectiveness in all stages of the value chain.
There are three main types of lean manufacturing:
-
Just-in-Time Manufacturing (JIT): This type of lean manufacturing is commonly referred to as "pull systems." JIT is a method in which components are assembled right at the moment of use, rather than being manufactured ahead of time. This approach aims to reduce lead times, increase the availability of parts, and reduce inventory.
-
Zero Defects Manufacturing (ZDM): ZDM focuses on ensuring that no defective units leave the manufacturing facility. Repairing a part that is damaged during assembly should be done, not scrapping. This applies to finished goods that may require minor repairs before shipment.
-
Continuous Improvement (CI), also known as Continuous Improvement, aims at improving the efficiency of operations through continuous identification and improvement to minimize or eliminate waste. Continuous improvement refers to continuous improvement of processes as well people and tools.