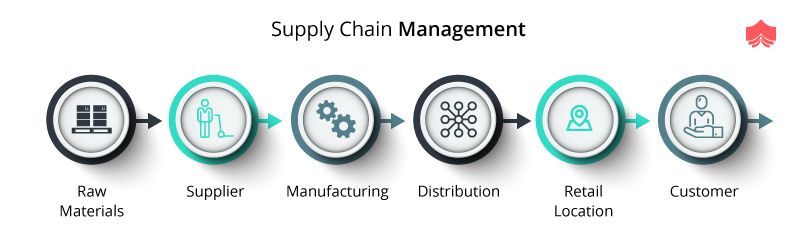
A single-piece flow production system can increase your output while decreasing your inventory and lead time. There are a few things to consider before implementing this technology. You'll need to measure the takt-time, which is the amount of time it takes to create an item. This allows you calculate the time it takes to make an item so that you can meet customer demand.
One-piece flow is best suited for manufacturing operations that are focused on low-variability goods. It is not the right fit for all businesses. To determine if this process is right for you, make sure that your metrics are accurate.
A more robust and scalable control system is required if you choose to use a single-piece flow. This will allow for a reduction in waste and increase efficiency. A one-piece item should be produced in a way that is easily scaleable to your customers' requirements. This will ensure the one-piece flow is not slower than traditional production.
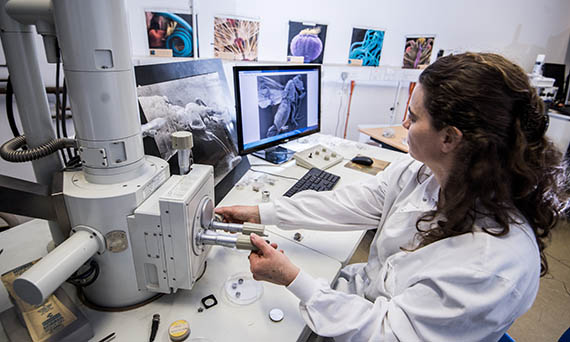
One-piece flow involves using a production line that looks similar to a U or S shape. It will allow for less movement from one step to the next. It also allows for greater assembly efficiency.
The lean process also has an associated term, the poka-yoke, which is a clever way to prevent defects from moving to the next step. This is an excellent way to save time while improving the quality and value of your products. The poka yoke is also a great way to reduce waste, inefficiency, and cost.
The one-piece flow process also works best when there is a high demand for individual products. In this case, you want to avoid wasting time and money by batching together different items from an order. A single flow for a work item will reduce delays and decrease inventory depreciation. This will reduce the time that your products are in storage or in work-in-progress (WIP) mode.
You can also use a single piece flow process to reduce the costs of maintaining your inventory. This is especially true for small businesses. This method allows you reduce your inventory storage and transport costs. This is a great way for you to cut down on the time that it takes to get your products to your customers.
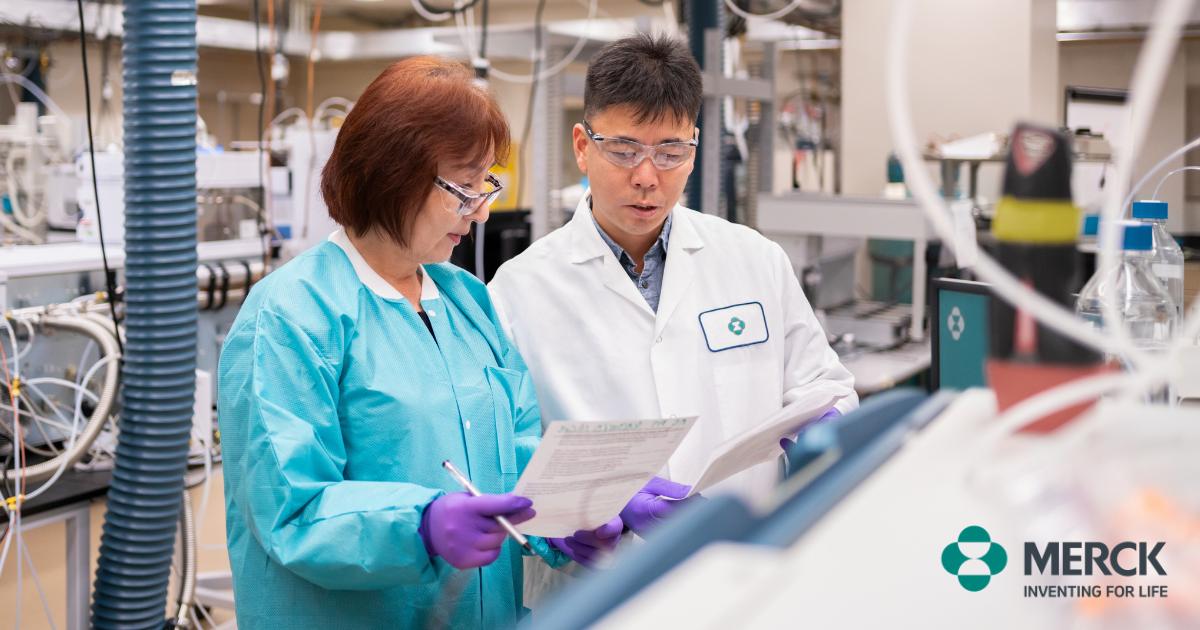
One-piece flow also increases employee morale because it allows employees to collaborate more closely. It also makes it easier to identify problems with your product. This is important as it could mean that your customers may receive defective or incomplete goods. This is a great opportunity to improve your customer service.
One-piece flow production lines can be used inside or outside an assembly line. This type of process can optimize your value stream. It allows for more efficient production and higher quality products. It's also a great way to cut costs and boost morale among employees.
FAQ
How can manufacturing avoid production bottlenecks
The key to avoiding bottlenecks in production is to keep all processes running smoothly throughout the entire production cycle, from the time you receive an order until the time when the product ships.
This includes planning for capacity requirements as well as quality control measures.
Continuous improvement techniques like Six Sigma are the best way to achieve this.
Six Sigma is a management method that helps to improve quality and reduce waste.
It focuses on eliminating variation and creating consistency in your work.
How can manufacturing efficiency improved?
First, we need to identify which factors are most critical in affecting production times. We then need to figure out how to improve these variables. If you don’t know where to begin, consider which factors have the largest impact on production times. Once you've identified them, try to find solutions for each of those factors.
What does it take for a logistics enterprise to succeed?
You need to have a lot of knowledge and skills to manage a successful logistic business. To communicate effectively with clients and suppliers, you must be able to communicate well. You must be able analyze data and draw out conclusions. You must be able manage stress and pressure under pressure. To increase efficiency and creativity, you need to be creative. You will need strong leadership skills to motivate and direct your team members towards achieving their organizational goals.
You must be organized to meet tight deadlines.
What type of jobs is there in logistics
There are many jobs available in logistics. Here are some examples:
-
Warehouse workers – They load and unload pallets and trucks.
-
Transportation drivers – These drivers drive trucks and wagons to transport goods and pick up the goods.
-
Freight handlers are people who sort and pack freight into warehouses.
-
Inventory managers – They manage the inventory in warehouses.
-
Sales representatives - They sell products to customers.
-
Logistics coordinators are responsible for organizing and planning logistics operations.
-
Purchasing agents are those who purchase goods and services for the company.
-
Customer service agents - They answer phone calls and respond to emails.
-
Ship clerks - They issue bills and process shipping orders.
-
Order fillers - These people fill orders based on what has been ordered.
-
Quality control inspectors are responsible for inspecting incoming and outgoing products looking for defects.
-
Others - There is a variety of other jobs in logistics. These include transportation supervisors and cargo specialists.
What is the difference between manufacturing and logistics
Manufacturing is the act of producing goods from raw materials using machines and processes. Logistics encompasses the management of all aspects associated with supply chain activities such as procurement, production planning, distribution and inventory control. It also includes customer service. Manufacturing and logistics are often considered together as a broader term that encompasses both the process of creating products and delivering them to customers.
Statistics
- It's estimated that 10.8% of the U.S. GDP in 2020 was contributed to manufacturing. (investopedia.com)
- Job #1 is delivering the ordered product according to specifications: color, size, brand, and quantity. (netsuite.com)
- According to the United Nations Industrial Development Organization (UNIDO), China is the top manufacturer worldwide by 2019 output, producing 28.7% of the total global manufacturing output, followed by the United States, Japan, Germany, and India.[52][53] (en.wikipedia.org)
- In 2021, an estimated 12.1 million Americans work in the manufacturing sector.6 (investopedia.com)
- (2:04) MTO is a production technique wherein products are customized according to customer specifications, and production only starts after an order is received. (oracle.com)
External Links
How To
How to Use the Just In Time Method in Production
Just-in-time is a way to cut costs and increase efficiency in business processes. This is where you have the right resources at the right time. This means that your only pay for the resources you actually use. Frederick Taylor first coined this term while working in the early 1900s as a foreman. After observing how workers were paid overtime for late work, he realized that overtime was a common practice. He decided to ensure workers have enough time to do their jobs before starting work to improve productivity.
JIT is about planning ahead. You should have all the necessary resources ready to go so that you don’t waste money. It is important to look at your entire project from beginning to end and ensure that you have enough resources to handle any issues that may arise. If you anticipate that there might be problems, you'll have enough people and equipment to fix them. This will prevent you from spending extra money on unnecessary things.
There are many JIT methods.
-
Demand-driven JIT: This is a JIT that allows you to regularly order the parts/materials necessary for your project. This will allow to track how much material has been used up. It will also allow you to predict how long it takes to produce more.
-
Inventory-based: This type allows you to stock the materials needed for your projects ahead of time. This allows you to predict how much you can expect to sell.
-
Project-driven : This is a method where you make sure that enough money is set aside to pay the project's cost. When you know how much you need, you'll purchase the appropriate amount of materials.
-
Resource-based: This is the most common form of JIT. This is where you assign resources based upon demand. If you have many orders, you will assign more people to manage them. If you don't have many orders, you'll assign fewer people to handle the workload.
-
Cost-based: This is similar to resource-based, except that here you're not just concerned about how many people you have but how much each person costs.
-
Price-based: This is a variant of cost-based. However, instead of focusing on the individual workers' costs, this looks at the total price of the company.
-
Material-based: This is quite similar to cost-based, but instead of looking at the total cost of the company, you're concerned with how much raw materials you spend on average.
-
Time-based: This is another variation of resource-based JIT. Instead of focusing only on how much each employee is costing, you should focus on how long it takes to complete your project.
-
Quality-based JIT is another variant of resource-based JIT. Instead of focusing on the cost of each worker or how long it takes, think about how high quality your product is.
-
Value-based JIT: One of the most recent forms of JIT. In this case, you're not concerned with how well the products perform or whether they meet customer expectations. Instead, you are focused on adding value to the marketplace.
-
Stock-based: This stock-based method focuses on the actual quantity of products being made at any given time. It's useful when you want maximum production and minimal inventory.
-
Just-in-time (JIT) planning: This is a combination of JIT and supply chain management. This refers to the scheduling of the delivery of components as soon after they are ordered. It's important because it reduces lead times and increases throughput.